Efficient Transformer Oil Filtration | High-Performance Machine.
Introduction
Welcome to the world of transformer oil filtration, the key to maximizing the performance and efficiency of your power transformers. In this article, we will explore the importance of this critical maintenance process and how it can significantly enhance the lifespan and reliability of your equipment.
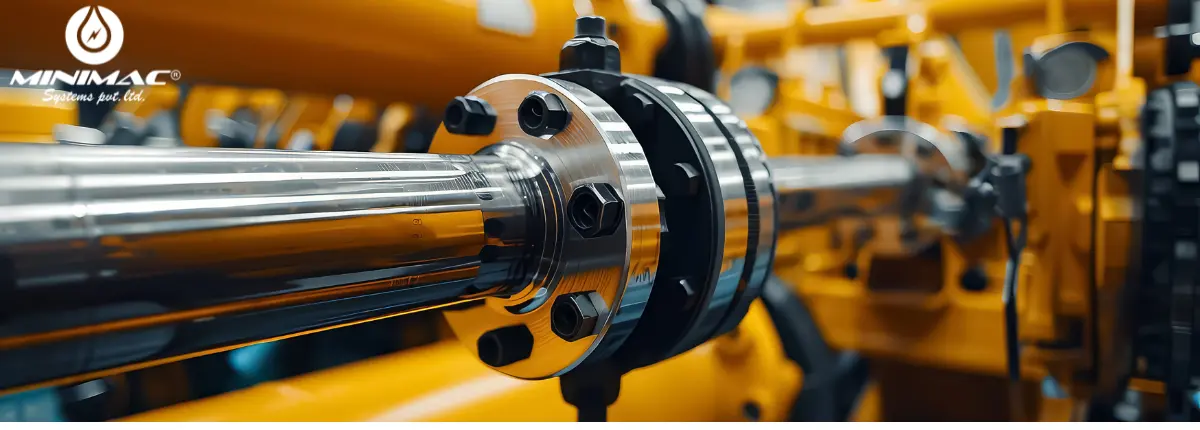
Transformer oil, also known as insulating oil, is responsible for several crucial functions in power transformers, such as heat dissipation, insulation, and arc quenching. Over time, however, contaminants and impurities can accumulate in the oil, compromising its effectiveness and putting your entire power system at risk.
That's where “Transformer Oil Filtration” comes into play. By removing contaminants, moisture, and gases from the oil, this process ensures optimal performance and extends the lifespan of your transformers. It not only eliminates the risk of costly breakdowns but also improves energy efficiency, reducing maintenance and downtime expenses.
At Minimac Systems, we understand the importance of maximizing performance and efficiency while minimizing operational costs. Our transformer oil filtration system is designed to deliver exceptional results, offering unmatched reliability and ensuring the smooth operation of your power transformers.
Experience the power of transformer oil filtration and take a transformative step towards optimal performance and long-lasting reliability of your power systems.
Importance of Transformer Oil Filtration:
Transformer oil plays a vital role in insulation, cooling, and protecting internal components. Over time, contaminants such as water, sludge, and oxidation by-products degrade the oil's properties, leading to inefficiency and potential failure. Regular oil filtration is essential to prevent costly breakdowns and prolong transformer life. Investing in an advanced filtration machine ensures your transformers operate reliably, minimizing maintenance costs and ensuring compliance with industry standards.
What is Transformer Oil Filtration?
Transformer oil filtration removes contaminants and restores the oil’s properties. The process involves coarse and fine filtration, vacuum dehydration, and degassing. This restores the oil's dielectric strength, maintains cooling efficiency, and prevents electrical failures. Regular filtration as part of a maintenance program reduces the need for frequent repairs, minimizes downtime, and ensures the reliable performance of the electrical system.
Benefits of Efficient Transformer Oil Filtration
- Improved Performance and Reliability:Removing impurities ensures better insulation and cooling, which enhance transformer reliability and reduce the risk of electrical failures.
- Extended Transformer Lifespan:Filtration slows down the aging process of transformer components, helping you avoid premature breakdowns and extend equipment life.
- Reduced Maintenance Costs:Efficient filtration decreases the frequency of oil changes and transformer repairs, leading to significant cost savings over time.
- Enhanced Energy Efficiency:Clean oil improves transformer efficiency, which reduces energy losses and operating costs while also lowering the organization’s carbon footprint.
- Regulatory Compliance: Maintaining clean oil through proper filtration helps meet industry standards and ensures the responsible operation of electrical infrastructure.
Common Contaminants in Transformer Oil
- Water:Even minimal water contamination can significantly reduce oil’s dielectric strength, leading to electrical failures and degraded insulation.
- Sludge:Formed due to oxidation, sludge can clog filters and hinder heat transfer, reducing cooling effectiveness.
- Oxidation By-products:Prolonged heat and oxygen exposure lead to varnish-like deposits that corrode components and compromise the oil's insulating properties.
- Particulate Matter: Dust, metal filings, and other particles in the oil cause abrasive wear on transformer parts, leading to more frequent maintenance.
- Dissolved gases:Gases like hydrogen and acetylene formed during transformer operation indicate internal issues and require immediate attention and filtration.
Understanding the Transformer Oil Filtration Process
- Coarse Filtration:This initial stage removes large particles like dust, metal filings, and sludge, protecting downstream filter components from clogging.
- Fine Filtration: In this stage, smaller contaminants like water, fine particulates, and oxidation by-products are removed, restoring the oil’s insulating properties.
- Vacuum Dehydration:his step extracts any remaining water from the oil, further enhancing its dielectric strength and preventing electrical issues.
Features of our Filtration Machine
- High-Efficiency Filtration:Our multi-stage system combines coarse and fine filtration, vacuum dehydration, and degassing to comprehensively remove contaminants, restoring oil to optimal condition.
- Automated Control System:The system is equipped with real-time monitoring and adjustments to maximize efficiency, reducing the need for manual intervention.
- Compact and Portable Design:Our machine’s design makes it easy to transport and set up at different locations, ensuring flexible and efficient on-site filtration.
- User-Friendly Interface:Operators can easily monitor and adjust settings through an intuitive control panel, minimizing errors and ensuring smooth operation.
- Robust Construction:Built to withstand tough industrial conditions, the machine is durable and requires minimal maintenance.
Steps to Efficiently Filter Transformer Oil
- Preparation:Ensure the transformer is isolated and the oil is at the correct temperature. Set up the necessary equipment and workspace.
- Coarse Filtration:Use a coarse filter to remove large contaminants like dust, metal filings, and sludge.
- Fine Filtration:Move on to fine filtration to eliminate smaller impurities, such as water and oxidation by-products, restoring the oil-insulating strength.
- Vacuum Dehydration: If needed, perform vacuum dehydration to remove any residual water from the oil.
- Degassing:In cases where dissolved gases are present, degassing will improve oil quality and performance.
- Continuous Monitoring:Track key parameters such as dielectric strength, water content, and dissolved gas levels to ensure that the oil meets the required specifications.
- Disposal and Recycling:Dispose of waste materials following environmental regulations. In some cases, the filtered oil may be reusable, contributing to sustainable maintenance practices.
Maintenance and Care for the Filtration Machine
Proper care and maintenance of your transformer oil filtration machine ensure long-term reliability and efficiency. Here’s how to maintain your equipment:
- Regular Inspections:Check for wear, damage, and changes in performance. Identifying issues early reduces the risk of malfunctions.
- Scheduled Maintenance: Follow the manufacturer’s maintenance schedule, including filter replacements and component lubrication, to ensure peak performance.
- Calibration and Testing:Regularly calibrate the machine’s sensors to ensure accurate monitoring and filtration.
- Operator Training:Ensure all operators are trained on the machine’s features, functions, and maintenance requirements to avoid user errors.
- Spare Parts Management:Keep an inventory of essential spare parts like filters, gaskets, and seals to avoid unnecessary downtime during repairs. By following these maintenance guidelines, you can ensure that your transformer oil filtration machine operates efficiently and remains reliable over the long term.
Conclusion
Investing in our transformer oil filtration system helps ensure your transformers operate efficiently with minimal downtime and reduced maintenance costs. With a multi-stage filtration process, user-friendly controls, and robust construction, our system is designed to meet the highest industry standards. Regular filtration keeps transformer oil clean, extends transformer lifespan, and optimizes energy efficiency. Choose our advanced filtration machine to safeguard your power systems and achieve long-lasting reliability.
FAQs:
- Improved transformer reliability: Clean oil ensures better insulation and cooling, reducing the risk of electrical failures.
- Extended transformer lifespan:Regular filtration slows down the aging process, extending the equipment's life.
- Reduced maintenance costs:Fewer oil changes and repairs lead to significant cost savings.
- Enhanced energy efficiency:Clean oil improves transformer efficiency, reducing energy losses and operating costs.
- Regulatory compliance:Maintaining clean oil helps meet industry standards and ensures responsible operation.
- Insulation: It insulates the transformer’s internal components, preventing electrical arcs and short circuits.
- Cooling: The oil absorbs heat generated by the transformer, dissipating it away from vital components.
- Arc Quenching: In the event of a fault, the oil helps quench any electrical arcs that occur, minimizing damage to the transformer.