High Viscosity in Lubrication: Benefits, Applications & Best Practices
Introduction to High Viscosity
Viscosity is the most crucial property of a lubricant, defining how well it performs under different operating conditions. It determines a lubricant’s ability to flow, resist shear, and provide an effective lubrication film between moving parts.
In many industrial applications, high-viscosity lubricants are essential for ensuring:
âś” Reduced friction and wear
âś” Better load-bearing performance
âś” Protection against extreme pressure and heat
High-viscosity oils and greases are widely used in heavy-duty machinery, particularly in gearboxes, bearings, turbines, and hydraulic systems that operate under extreme loads and harsh conditions. Understanding how viscosity impacts lubrication is crucial to maintaining machinery efficiency and longevity.
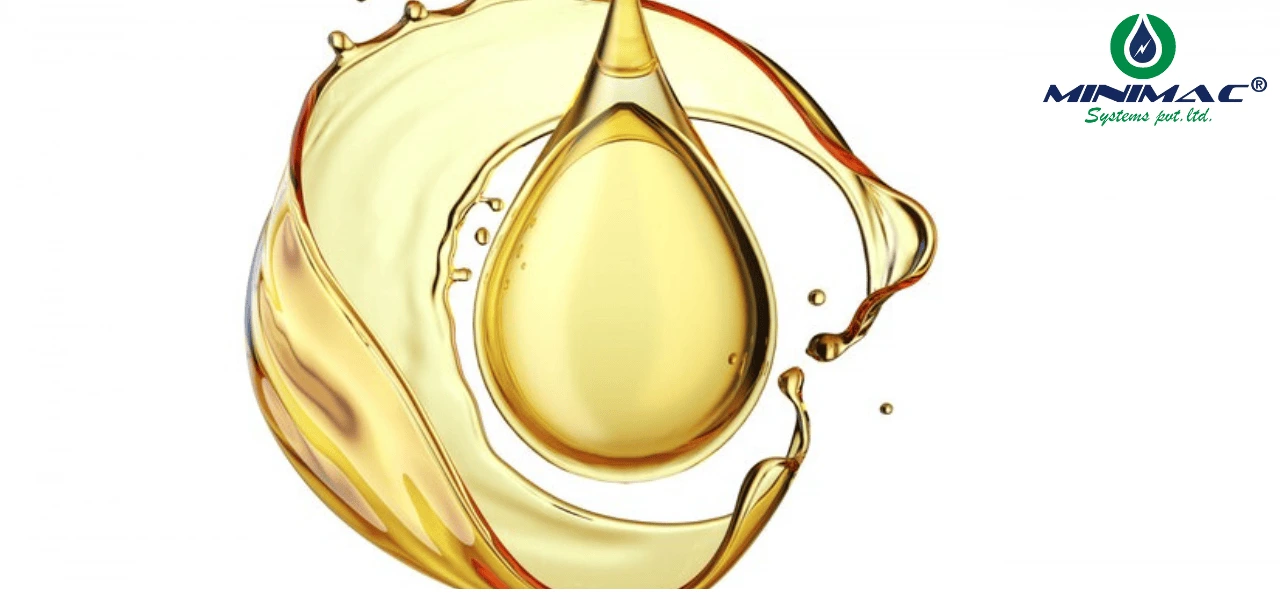
The Science Behind Viscosity in Lubrication
What is Viscosity?
Viscosity is the measure of a fluid’s resistance to flow. In simpler terms:
- Low-viscosity oils flow easily and are suitable for high-speed machinery.
- High-viscosity oils are thicker, providing better lubrication film strength and wear resistance.
The Viscosity Index determines how much a lubricant’s viscosity changes with temperature. A high viscosity index lubricant maintains stability across temperature variations, making it suitable for extreme environments.
The Role of Viscosity in High-Velocity Applications
Kinematic Viscosity vs. Dynamic Viscosity
Viscosity is a critical property that affects high-velocity lubrication. There are two primary types:
- Kinematic viscosity measures how a fluid resists motion under gravitational forces. It is vital in fluid flow studies.
- Dynamic viscosity refers to a fluid’s resistance to shear stress, influencing drag and aerodynamic behavior.
Reynolds Number and Its Influence on High Velocity
The Reynolds number determines whether fluid flow is laminar or turbulent. It is a dimensionless quantity used to predict flow patterns at different velocities.
- Efficient fluid dynamics
- Reduced turbulence
- Lower energy loss due to drag
Impact on Fluid Flow and Fluid Dynamics
In high-velocity lubrication, selecting the right viscosity ensures minimal drag while maintaining a strong lubrication film. Low viscosity improves fluid flow, whereas higher dynamic viscosity enhances load-bearing capacity.
Why is High Viscosity Important?
In high-load, slow-speed applications, metal surfaces are under extreme stress. A high-viscosity lubricant prevents direct metal-to-metal contact, reducing friction, wear, and energy loss.
Key Benefits of High-Viscosity Lubricants
1. Improved Wear Protection
High-viscosity lubricants form a thicker protective layer, minimizing wear on components like gears, bearings, and hydraulic pistons. This ensures longer machine life and reduced maintenance costs.
12. Superior Load-Carrying Capacity
Industrial machinery often experiences heavy shock loads. High-viscosity gear oils and EP (Extreme Pressure) greases prevent breakdown under high stress, maintaining smooth operation even in harsh conditions.
3. Stronger Lubrication Film
A high-viscosity lubricant maintains a robust oil film, preventing surface fatigue and scuffing in applications like wind turbine gearboxes, mining equipment, and steel mills.
4. Resistance to Extreme Conditions
Industries like power generation, construction, and metallurgy expose lubricants to high temperatures, pressure, and contaminants. High-viscosity synthetic oils resist thermal degradation, oxidation, and sludge formation, ensuring optimal performance.
Applications of High-Viscosity Lubricants
1. Industrial Gearboxes
Gearboxes operate under high torque and continuous load, requiring high-viscosity gear oils to:
- Prevent gear tooth wear
- Reduce micro pitting and scuffing
- Ensure efficient power transmission
2. Heavy-Duty Bearings
High-viscosity greases are essential for slow-moving, high-load bearings found in:
- Steel plants
- Mining conveyors
- Cement kilns
These lubricants provide superior adhesion, reducing bearing failures and replacement costs.
3. High-Temperature Equipment
In power plants, refineries, and aerospace applications, machinery operates at extreme temperatures. Synthetic high-viscosity oils prevent:
- Thermal breakdown
- Sludge formation
- Oxidation-related failures
4. Slow-Speed Machinery
For applications like open gears, worm gears, and heavy presses, high-viscosity lubricants improve:
- Film thickness to prevent metal-to-metal contact
- Load distribution to reduce stress concentration
Challenges of High-Viscosity Lubrication
Despite their benefits, high-viscosity lubricants have some challenges:
1. Energy Efficiency Concerns
Thicker oils increase fluid resistance, leading to higher energy consumption in hydraulic and circulation systems.
2. Cold-Start Issues
In low temperatures, high-viscosity lubricants become stiff, affecting:
- Pump ability
- Startup lubrication
- Oil circulation
Solution:Use multi-grade or synthetic oils that provide better cold-flow properties.
How to Select the Right High-Viscosity Lubricant
Choosing the correct viscosity is critical for optimal machinery performance. Consider these key factors:
1. Operating Temperature
- For high temperatures: Choose a high-viscosity index lubricant to prevent thinning.
- For cold environments: Use synthetic lubricants for better flowability.
2. Load and Speed Conditions
- High load, slow speed: Require higher viscosity for better film strength.
- Low load, high speed: Need lower viscosity to reduce frictional losses.
3. Manufacturer Recommendations
- Always refer to OEM (Original Equipment Manufacturer) guidelines for optimal performance.
4. Lubricant Additives
Look for:
- Anti-wear (AW) additives for reducing friction
- Extreme Pressure (EP) additives for heavy loads
- Oxidation inhibitors to enhance lubricant life
Conclusion
High-viscosity lubricants play a crucial role in protecting industrial machinery, extending service life, and enhancing performance. They offer better film strength, wear resistance, and thermal stability, making them ideal for gearboxes, bearings, and heavy-duty applications.
However, selecting the right viscosity grade is key to balancing energy efficiency and lubrication performance. Industries must consider operating conditions, manufacturer recommendations, and additive formulations to achieve optimal equipment reliability.
For expert guidance on high-viscosity lubrication solutions, consult with a professional lubrication specialist today!
FAQs:
- High-viscosity lubricants are thicker, providing better load support.
- Low-viscosity lubricants flow easily, reducing frictional resistance in high-speed applications.