How to Maintain Lubricant Viscosity for Optimal Machinery Performance
Introduction to Lubricant Viscosity
Lubricant Viscosity is the measure of a lubricant’s resistance to flow. It determines how well the lubricant can form a protective film between moving components, reducing friction and wear. The viscosity of an oil or grease is crucial for ensuring smooth machinery operation and optimal performance across various industrial applications.
Different types of lubricants have varying viscosity grades. Hydraulic Oil Viscosity is essential for efficient energy transfer in hydraulic systems, while Gear Oil Viscosity ensures proper load distribution and wear protection in heavily loaded gears. If Oil Viscosity is not maintained, it can lead to increased wear, overheating, and even complete Oil Breakdown, causing machinery failure.
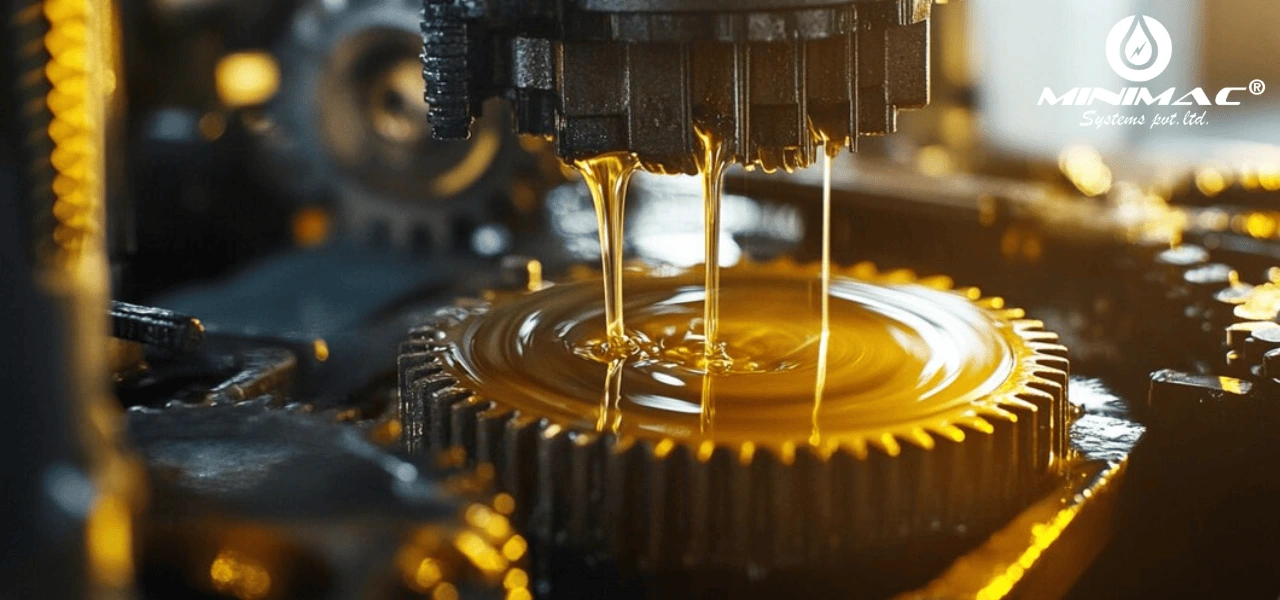
Why Viscosity Maintenance is Crucial
Maintaining the correct Lubricant Viscosity is essential for several reasons:
- Prevent Lubricant Breakdown: Lubricants degrade over time due to contamination, heat, and oxidation, leading to Viscosity Degradation and loss of protective properties.
- Reduce Friction and Wear: Proper Oil Viscosity ensures that machinery components remain lubricated, preventing metal-to-metal contact.
- Enhance Energy Efficiency: Maintaining the right Hydraulic Oil Viscosity ensures efficient power transfer in hydraulic systems, while optimal Gear Oil Viscosity reduces energy losses in gear mechanisms.
- Extend Oil Change Intervals: Monitoring Oil Viscosity and taking corrective actions can help extend Oil Change Intervals, reducing operational costs.
If Viscosity Loss occurs due to factors like contamination or oxidation, the lubricant loses its ability to protect machinery, leading to premature failure and costly downtime.
Factors Leading to Viscosity Degradation
Several environmental and operational factors contribute to Viscosity Degradation and Oil Breakdown. Understanding these causes can help prevent performance issues.
1. Temperature Fluctuations
- High temperatures cause lubricants to thin out, reducing their load-bearing capacity. This is particularly crucial for Hydraulic Oil Viscosity, as hydraulic systems require stable viscosity for precise operation.
- Extremely low temperatures, on the other hand, can cause lubricants to thicken, reducing fluidity and increasing energy consumption.
2. Contamination
- Water contamination leads to emulsification, breaking down the lubricant’s molecular structure and accelerating Viscosity Degradation.
- Dirt, metal particles, and other contaminants disrupt Oil Viscosity, leading to increased wear and tear.
- Fuel dilution is a common issue in engines, causing Lubricant Breakdown and reduced viscosity.
3. Mechanical Shear
- In high-pressure environments, such as gearboxes and hydraulic systems, lubricants experience intense mechanical stress. Over time, this shearing effect leads to Viscosity Loss, compromising the lubricant’s protective properties.
4. Additive Depletion
- Many lubricants contain special additives to maintain Oil Viscosity, but these additives break down over time. This is why monitoring lubricant condition through Oil Analysis is critical for maintaining performance.
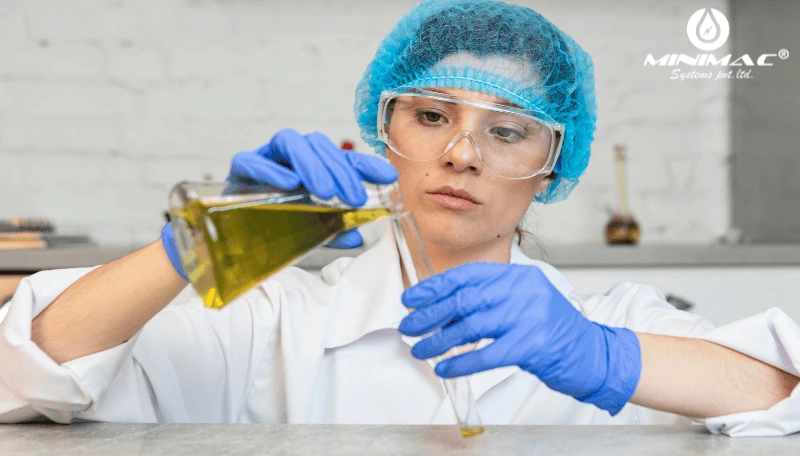
Best Practices for Preventing Viscosity Loss
To ensure stable Lubricant Viscosity, follow these best practices:
1. Choose the Right Lubricant for Your Application
- Use lubricants with the appropriate Hydraulic Oil Viscosity to match your system’s pressure and temperature requirements.
- Select Gear Oil Viscosity based on load conditions to prevent excessive wear.
2. Control Operating Temperature
- Use cooling systems to prevent lubricants from overheating and degrading.
- Ensure adequate insulation in cold environments to maintain stable Oil Viscosity.
- Use synthetic lubricants with a high Viscosity Index, which helps them remain stable across a wide temperature range.
3. Prevent Contamination
- Install advanced filtration systems to remove particulates and moisture from the lubricant.
- Store lubricants in sealed containers to prevent exposure to dust and humidity.
- Regularly check for signs of contamination through Oil Analysis.
4. Optimize Oil Change Intervals
- Follow data-driven Oil Change Intervals instead of fixed schedules.
- Conduct periodic Oil Analysis to determine if the lubricant is still effective.
- Extend Oil Change Intervals using high-performance lubricants and Viscosity Improvers.
The Role of Viscosity Improvers in Maintaining Stability
Viscosity Improvers are chemical additives designed to maintain a lubricant’s viscosity across varying temperatures. They are particularly useful in applications where extreme temperature fluctuations occur.
How Viscosity Improvers Help:
- They prevent lubricants from thinning out at high temperatures, ensuring stable Lubricant Viscosity.
- They reduce excessive thickening in cold conditions, which is crucial for maintaining Oil Viscosity.
- They enhance the overall durability of lubricants, helping to prevent Viscosity Loss.
Regularly replenishing Viscosity Improvers can help maintain Oil Viscosity and extend Oil Change Intervals, reducing lubricant consumption and operational costs.
Importance of Oil Analysis and Monitoring
Oil Analysis is one of the most effective ways to track Viscosity Loss and detect early signs of Oil Breakdown. Conducting routine Oil Analysis helps identify potential issues before they lead to machinery failure.
Key Oil Analysis Tests:
- Kinematic Viscosity Test: Measures how easily a lubricant flows under standard conditions.
- Viscosity Index Measurement: Evaluate how well a lubricant maintains its viscosity at different temperatures.
- Contamination Analysis: Detects contaminants such as water, dirt, and fuel that cause Viscosity Degradation.
By incorporating Oil Analysis into a preventive maintenance program, industries can optimize Oil Change Intervals, prevent Lubricant Breakdown, and maximize machinery performance.
Conclusion
Maintaining Lubricant Viscosity is essential for ensuring machinery efficiency, reducing wear, and preventing Viscosity Loss. By selecting the right lubricants, preventing contamination, using Viscosity Improvers, and conducting regular Oil Analysis, industries can minimize Viscosity Degradation and extend Oil Change Intervals effectively.
FAQs:
- Viscometers: Devices such as kinematic viscometers, rotational viscometers, and capillary viscometers measure how easily oil flows.
- Kinematic Viscosity Test: Determines viscosity by measuring the time it takes for a specific volume of oil to flow through a capillary under gravity.
- Saybolt Universal Viscometer (SUV): Measures the time required for oil to pass through a calibrated orifice.
- Brookfield Viscometer: A rotating spindle is used to measure resistance and determine viscosity.
- Adding Viscosity Improvers: Special additives help maintain viscosity at varying temperatures.
- Using a Higher Viscosity Grade Oil: Switching to a lubricant with a higher base viscosity.
- Reducing Contamination: Removing water, fuel, or solvents that dilute the oil.
- Lowering Operating Temperature: Excess heat can reduce viscosity; using coolers or synthetic oils helps maintain stability.
- Density refers to mass per unit volume, while viscosity measures resistance to flow.
- Higher-density fluids generally have higher viscosity, but this is not always the case.
- Oil Viscosity is affected more by temperature and additives than density alone.
- Use a Lower Viscosity Grade Oil: Switching to a lubricant with lower base viscosity helps reduce resistance to flow.
- Add Diluting Agents: Some formulations include viscosity reducers.
- Increase Operating Temperature: Heating oil reduces its viscosity, improving flowability.
- Use Synthetic Lubricants: Some synthetics have better fluidity at lower viscosities.
- High temperatures make the oil thinner, reducing its ability to form a protective film.
- Low temperatures make the oil thicker, which can cause flow resistance and startup issues.
- Viscosity Improvers help stabilize viscosity across different temperature ranges.
- It ensures proper lubrication, reducing wear and friction.
- It prevents Oil Breakdown and Viscosity Loss, extending lubricant life.
- It optimizes Hydraulic Oil Viscosity for efficient energy transfer.
- It maintains Gear Oil Viscosity for smooth gear operation and load distribution.
- It reduces overheating and improves energy efficiency.
- Viscosity decreases, meaning the oil becomes thinner and flows more easily.
- This can lead to Viscosity Loss, reducing lubrication efficiency.
- High temperatures accelerate Viscosity Degradation, potentially leading to Oil Breakdown.
- Use Viscosity Improvers: These additives help keep viscosity stable across temperatures.
- Conduct Regular Oil Analysis: Helps detect Viscosity Loss early.
- Optimize Oil Change Intervals: Prevents degradation before it affects viscosity.
- Control Temperature: Prevent excessive heat or cold exposure.
- Prevent Contamination: Use filtration to remove dirt, water, and fuel dilution.
- Kinematic Viscosity Test: Measures oil flow through a capillary tube at a controlled temperature.
- Brookfield Viscometer Test: Determines dynamic viscosity by rotating a spindle in the oil.
- Saybolt or Redwood Viscometer: Measures time for a set volume of oil to flow through an orifice.
- ASTM Viscosity Tests: Standardized tests like ASTM D445 ensure precise viscosity measurements.