Pareto Principle in Maintenance: How the 80/20 Rule Reduces Downtime.
Introduction:
The Pareto Principle, also known as the 80/20 rule, is a simple yet powerful concept that
applies to various areas, including maintenance. Named after the Italian economist Vilfredo
Pareto, the principle suggests that 80% of results come from 20% of causes. In the context of
maintenance, this means that a small proportion of machines or factors often contribute to the
majority of downtime.
By identifying and focusing on the critical 20%, companies can significantly improve efficiency,
reduce unnecessary costs, and extend the lifespan of machinery and equipment.
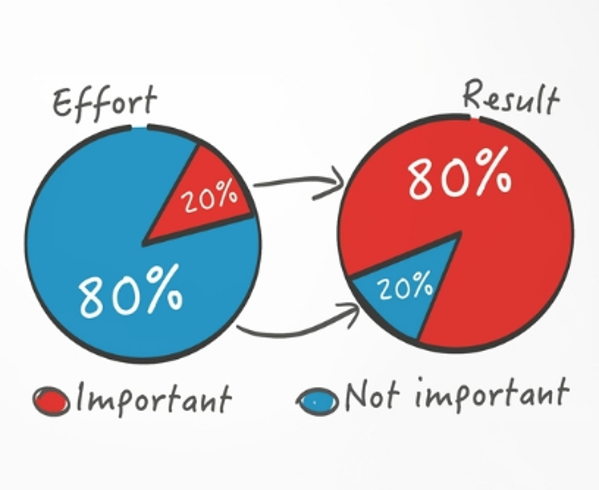
We at Minimac study your maintenance needs and provide the highest quality & service quality solutions. Call +91 7030901266 for Mechanical Maintenance & Oil Check.
The 80/20 Rule in Maintenance
In maintenance, the Pareto Principle states that 80% of maintenance issues or downtimes arise
from only 20% of the causes or machines. This insight can help businesses prioritize their
efforts, ensuring that limited resources—whether financial, time, or personnel—are allocated
efficiently to areas that will have the most significant impact.
By targeting the root causes of downtime, maintenance teams can streamline processes, optimize
equipment reliability, and ultimately improve overall productivity.
the Downtime.
Key Causes of Downtime in Maintenance
Few key causes that constitute this 20% are: Let’s explore the 20% of factors that contribute to the majority of downtime in maintenance operations. Identifying these causes is crucial for improving efficiency and reducing maintenance costs.
1. Particle Contamination
One of the leading causes of machine failure is particle contamination. Small particles, like dust, dirt, or metal shavings, can cause friction, leading to wear and tear in machinery components. This type of contamination is especially harmful in lubrication systems, where it can affect oil flow, create blockages, and damage internal parts.
Preventive Measures:
- Regular oil filtration and monitoring.
- Installing filtration systems like Minimac Systems’ Oil Filtration Systems.
- Use of clean room environments and sealed equipment.
2. Moisture Contamination
Water contamination in lubricants or hydraulic systems can cause corrosion, rusting, and poor lubrication performance. Excess moisture may also degrade the lubricant, leading to higher friction and wear.
Preventive Measures:
- Using moisture removal filters.
- Monitoring humidity levels in the environment.
- Regular checks for water contamination levels in lubricants.
3. Wrong/Degraded Lubricant
Using the wrong type of lubricant or degraded lubricants can severely impact machinery performance. Over time, lubricants lose their viscosity and ability to protect against friction, causing components to wear out prematurely.
Preventive Measures:
- Regular lubricant analysis and replacement.
- Use of high-quality, application-specific lubricants.
- Following manufacturer’s lubrication guidelines.
4. Misalignment
Misalignment of machine parts, such as shafts or gears, creates excessive vibration, leading to more severe mechanical issues and costly repairs. Vibration analysis or regular inspections can often detect this problem.
Preventive Measures:
- Misalignment of machine parts, such as shafts or gears, creates excessive vibration, leading to more severe mechanical issues and costly repairs. Vibration analysis or regular inspections can often detect this problem.
- Use of advanced monitoring equipment like vibration sensors.
5. Imbalance
Imbalanced machinery can lead to vibrations, increased wear, and eventual failure. Imbalance often arises from worn-out bearings, improper assembly, or damage to rotating components.
Preventive Measures:
- Regular balancing of equipment.
- Monitoring and replacing worn-out components before they cause damage.
6. High Temperature
Excessive heat is a major factor that accelerates wear and tear in machinery. It can cause lubricants to break down, increase friction, and damage seals or gaskets. Overheated equipment is more prone to failure and breakdown.
Preventive Measures:
- Monitoring operating temperatures and ensuring they remain within optimal ranges.
- Use of cooling systems or heat exchangers.
- Regular maintenance of cooling equipment and fans.
How to Implement the Pareto Principle in Maintenance
To implement the Pareto Principle in maintenance, organizations need to perform a thorough analysis of their machinery and identify the top causes of downtime. Here's a step-by-step approach:
- Step 1: Collect data on equipment failures and downtime.
- Step 2: Identify the top causes of downtime (the 20% that contribute to 80% of the problems).
- Step 3: Prioritize addressing these critical issues, focusing resources and maintenance efforts on the high-impact areas.
- Step 4: Continuously monitor results and adjust strategies to improve machine reliability.
Benefits of Focusing on Critical 20%
Focusing on the critical 20% of causes that contribute to the majority of downtime offers several advantages:
- Reduced Downtime: By addressing the root causes, machines operate more reliably, leading to fewer breakdowns.
- Cost Savings: Reducing downtime means fewer repair costs and less unplanned maintenance.
- Extended Equipment Life: Preventive maintenance ensures that machines last longer, improving return on investment (ROI)
- Improved Efficiency: Streamlined operations result in higher productivity and lower operational costs.
How Minimac Systems Can Help in Reducing Downtime
Minimac Systems specializes in providing advanced lubrication and filtration solutions that target key maintenance issues. Our products, such as oil filtration systems and hydraulic oil flushing systems, help reduce contamination, improve lubricant life, and enhance equipment reliability. By integrating Minimac’s technology, companies can tackle the critical 20% of issues that contribute to most downtimes, ensuring smoother operations and better performance.
Conclusion
The Pareto Principle offers a simple yet effective framework for improving maintenance strategies. By focusing on the critical 20% of causes, businesses can dramatically reduce downtime, enhance equipment reliability, and achieve long-term cost savings. Incorporating targeted solutions like Minimac Systems’ oil filtration and lubrication management products helps in addressing the root causes of downtime, ultimately improving overall productivity and performance.