Understanding the Unit of Viscosity: A Key Parameter in Lubrication
Introduction to Viscosity
Viscosity is a fundamental property of fluids that defines their resistance to flow. It is a measure of how easily a fluid moves when subjected to force. The concept of viscosity plays a crucial role in various industries, especially lubrication, where selecting the right viscosity level ensures the proper functioning and longevity of mechanical systems.
Viscosity is primarily classified into two types: absolute viscosity (dynamic viscosity) and kinematic viscosity. Understanding their units and differences helps in choosing the right lubricant for industrial applications.
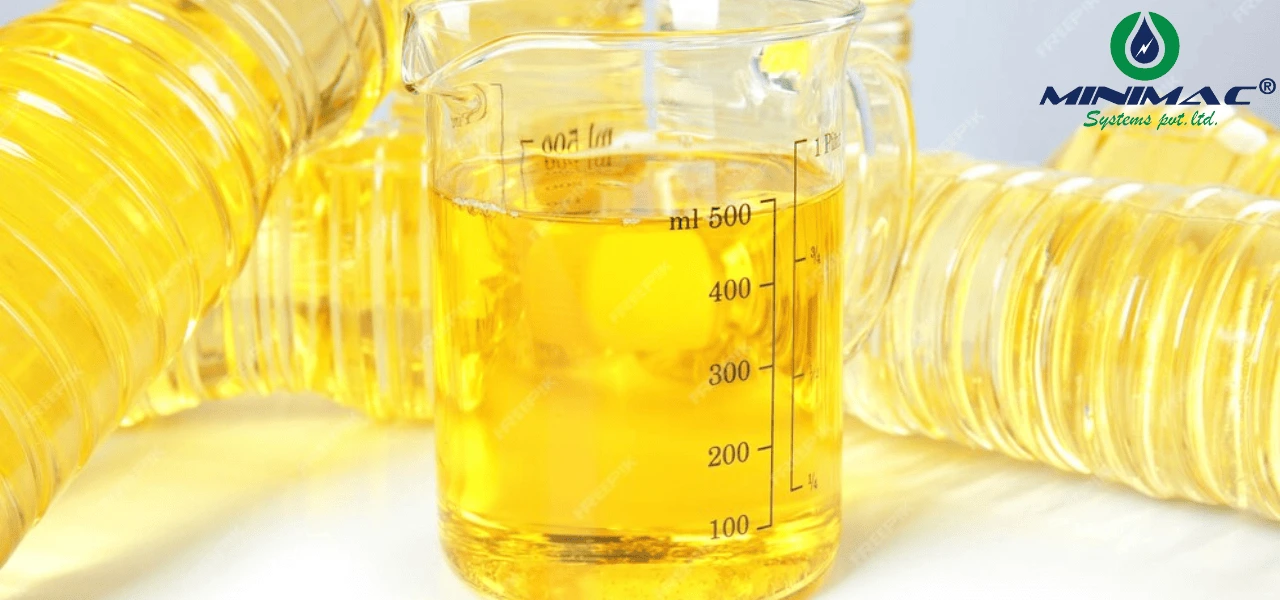
Importance of Viscosity in Lubrication
In lubrication, viscosity determines how effectively a lubricant can separate moving components, reducing friction, preventing wear, and minimizing energy loss. Using the wrong viscosity lubricant can lead to either inadequate protection (if too low) or increased drag and energy consumption (if too high).
For industrial machinery, oil and grease formulations are selected based on viscosity SI units and standardized measurement systems like ISO VG (Viscosity Grade) and SAE (Society of Automotive Engineers) viscosity grades.
Viscosity SI Units and Other Measurement Units
Viscosity is measured using several units depending on whether it is dynamic viscosity or kinematic viscosity.
Dynamic Viscosity (Absolute Viscosity) Units
- SI Unit: Pascal-second (Pa·s) or milliPascal-second (mPa·s)
- CGS Unit: Poise (P) or centipoise (cP), where 1 P = 0.1 Pa·s
- Common Industrial Use: Centipoise (cP) is frequently used in lubrication industry applications.
Kinematic Viscosity Units
- SI Unit: Square meter per second (m²/s)
- CGS Unit: Stokes (St) or centistokes (cSt), where 1 St = 10⁻⁴ m²/s
- Common Industrial Use: Centistokes (cSt) is the most widely used unit in industrial lubrication, with ISO VG ratings based on kinematic viscosity at 40°C.
Understanding Absolute Viscosity (Dynamic Viscosity)
Absolute viscosity, also known as dynamic viscosity, refers to a fluid’s resistance to shear stress. It measures the force required to move one layer of fluid over another.
Formula:
Where:
- = dynamic viscosity (Pa·s or cP)
- = applied force (N)
- = area of the fluid layer (m²)
- = velocity gradient (s⁻¹)
Dynamic viscosity is used to determine how a lubricant behaves under mechanical stress and is critical in applications involving gears, hydraulics, and compressors.
Understanding Kinematic Viscosity
Kinematic viscosity is the ratio of dynamic viscosity to the density of the fluid. It represents how fast a fluid flows under gravity.
Formula:
- = kinematic viscosity (m²/s or cSt)
- = dynamic viscosity (Pa·s or cP)
- = density of the fluid (kg/m³)
Kinematic viscosity is widely used in industrial lubrication standards such as ISO VG ratings, which categorize lubricants based on their kinematic viscosity at 40°C
Viscosity vs. Kinematic Viscosity
While dynamic viscosity measures a fluid’s internal resistance to movement, kinematic viscosity considers both viscosity and fluid density. In lubrication, the kinematic viscosity-to-viscosity relationship helps in determining how a lubricant will behave under real-world operating conditions.
Key Differences:
Property | Dynamic Viscosity | Kinematic Viscosity |
---|---|---|
Definition | Resistance to shear stress | Ration of dynamic viscosity to density |
Unit | Pa.s or cP | m²/s or cSt |
Measurement | Require force application | Measurement using gravity-driven flow |
Coefficient of Viscosity Unit and Its Role
The coefficient of viscosity represents the relationship between shear stress and shear rate in a fluid. It is often synonymous with dynamic viscosity in Newtonian fluids. The coefficient of viscosity is crucial in industries where precise viscosity control is required for operations like metalworking, automotive lubrication, and hydraulic systems.
Viscosity Measurement Units and Techniques
Measuring viscosity requires specialized instruments that ensure accuracy in selecting the right lubricant.
Common Viscosity Measurement Techniques:
- Capillary Viscometers (Ubbelohde, Ostwald) – Used for kinematic viscosity.
- Rotational Viscometers (Brookfield Viscometer) – Measures dynamic viscosity.
- Falling Ball Viscometer – Determines viscosity by measuring the falling speed of a ball through the fluid.
- Redwood and Saybolt Viscometers – Used in petroleum industries.
Each method provides valuable insights into the viscosity behavior of lubricants under different conditions.
Conclusion
Understanding viscosity measurement units and their significance in lubrication is crucial for selecting the right lubricant. Absolute viscosity (dynamic viscosity) and kinematic viscosity serve different purposes but are interrelated. By using viscosity SI units like Pascal-seconds and centistokes, industries can ensure optimal lubrication performance, reduce wear, and enhance machinery longevity.
FAQs:
- Dynamic Viscosity: Pascal-second (Pa·s) in SI units and Poise (P) in CGS units.
- Kinematic Viscosity: Square meter per second (m²/s) in SI units and Stokes (St) in CGS units.
- Dynamic Viscosity: Pascal-second (Pa·s)
- Kinematic Viscosity: Square meter per second (m²/s)
- Dynamic Viscosity: SI unit is Pascal-second (Pa·s) with the dimension ML⁻¹T⁻¹.
- Kinematic Viscosity: Square meter per second (m²/s)