Unveiling the Power: Exploring the Importance of Transformer Oil Testing.
Introduction
Transformers are crucial components in the efficient delivery of electricity. Ensuring their optimal performance and longevity is essential for reliable power distribution. One key factor in maintaining transformers is regular oil testing. This article delves into the importance of oil testing in transformers and the significant benefits it offers.
Importance of Oil Testing in Transformers
Oil testing serves as a diagnostic tool to evaluate the condition of the insulating oil used in transformers. By analyzing the oil’s composition and properties, experts can detect potential issues such as contamination, oxidation, or degradation. This enables early detection of problems, facilitating timely preventive maintenance or repairs.
Regular oil testing provides multiple advantages:
In conclusion, oil testing is an indispensable practice for ensuring the reliability and longevity of transformers. By leveraging oil analysis, companies can proactively address potential problems, optimize performance, and ultimately save significant costs in the long run.
Why is Oil Testing Important for Transformers?
Transformers are the backbone of modern electrical power systems, playing a crucial role in the efficient transmission and distribution of electricity. These vital components rely on insulating oil to maintain performance and longevity. The insulating oil not only acts as an electrical insulator but also helps dissipate heat generated during the transformer's operation. Over time, this oil can become contaminated, oxidized, or degraded, leading to issues that compromise the transformer’s functionality and may result in catastrophic failures.
Oil testing provides a comprehensive evaluation of the oil's condition, allowing for the early detection of potential issues. By analyzing the oil’s physical, chemical, and electrical properties, experts can identify abnormalities or changes that may indicate underlying problems within the transformer. This proactive approach enables timely preventive maintenance, repairs, or replacements, ultimately enhancing the transformer’s reliability and extending its service life.
Furthermore, oil testing is a critical component of a transformer’s health monitoring and maintenance program. By regularly assessing the oil’s condition, operators can make informed decisions about the transformer’s operational status and maintenance requirements. This helps minimize the risk of unexpected failures and ensures the reliable delivery of electricity to end-users.
Types of Tests Conducted in Oil Testing
Oil testing includes a variety of analytical procedures designed to evaluate the condition and properties of insulating oil in transformers. These tests can be categorized into the following key areas:
- Physical Tests:Focus on the oil’s physical characteristics, such as color, appearance, viscosity, and dielectric strength. These parameters can indicate contamination, oxidation, or degradation of the oil.
- Chemical Tests:Chemical analysis provides insights into the oil’s composition and the presence of contaminants or byproducts. Tests such as dissolved gas analysis (DGA), acid number measurement, and water content determination can help identify issues like overheating, partial discharges, or moisture presence.
- Electrical Tests:Evaluate the oil’s electrical properties, such as dielectric breakdown voltage, power factor, and resistivity. These tests determine the oil’s ability to withstand electrical stress and provide early warning signs of potential insulation failures.
Understanding BDV Testing
One critical electrical test in oil testing is the Dielectric Breakdown Voltage (BDV) Test. The BDV test measures the voltage at which the oil loses its insulating properties and allows an electric current to pass through. This test determines the oil’s ability to withstand electrical stress and detect contaminants like water, dirt, or particles that may reduce its insulating performance.
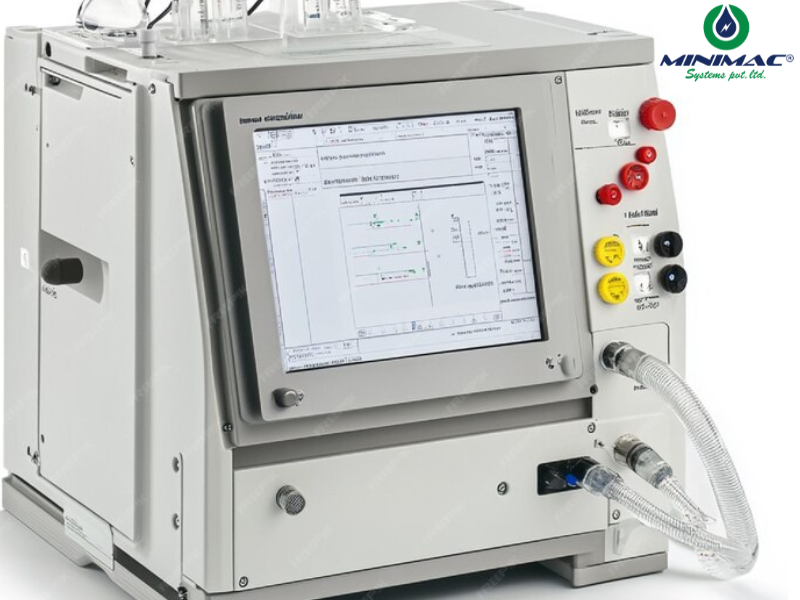
The BDV test uses a specialized apparatus that gradually increases the voltage applied to the oil sample until breakdown occurs.
A low BDV value indicates reduced insulating capacity due to contamination or deterioration. Regular BDV testing ensures that the oil maintains its dielectric strength, allowing the transformer to operate safely under various electrical loads.
Maintaining a high BDV value allows transformers to operate more reliably and efficiently, minimizing the risk of insulation failure and unexpected downtime. As part of a comprehensive oil testing program, BDV testing provides a clear indication of the oil’s health and supports informed maintenance decisions.
Benefits of Regular Oil Testing
Regular oil testing offers a multitude of benefits for transformer owners and operators, making it an essential component of a comprehensive asset management strategy:
- Early Problem Detection:Regular monitoring allows for early identification of potential issues like contamination, oxidation, or degradation, enabling timely preventive maintenance or corrective actions.
- Optimization of Maintenance Strategies:Oil testing provides data that can be used to optimize the transformer’s maintenance schedule, ensuring efficient resource allocation and peak performance.
- Improved Reliability and Lifespan:Addressing issues identified through oil testing helps extend the equipment’s lifespan and enhance its overall reliability, reducing the need for costly replacements.
- Cost Savings:Regular oil testing can lead to significant cost savings by proactively addressing problems before they escalate, avoiding high expenses associated with emergency repairs, unplanned downtime, and premature equipment replacement.
Common Issues Detected Through Oil Testing
Oil testing is a powerful tool for identifying a wide range of issues that can affect the performance and longevity of transformers. Some common problems detected through oil analysis include:
- Contamination: Foreign particles, such as dirt, moisture, or metal particles, can compromise the oil’s insulating properties, leading to increased electrical stress.
- Oxidation:Over time, insulating oil can oxidize, forming sludge, varnish, and other byproducts that impair cooling and insulating capabilities.
- Thermal Degradation:Excessive heat can break down the oil, forming gases and byproducts that indicate overheating or insulation failure.
- Partial Discharges: Localized electrical discharges can be detected through oil testing, indicating insulation issues or maintenance needs.
Frequency of Oil Testing
The frequency of oil testing depends on the transformer’s size, age, and operating conditions. For smaller transformers, testing may be conducted annually or every two years. However, for larger, more critical transformers, more frequent testing, semi-annually or quarterly is typically recommended.
Factors such as operating environment, load conditions, and any known issues can also influence testing frequency. For example, transformers in harsh environments or under high-stress conditions may require more frequent testing to ensure reliable performance.
Oil Testing Methods and Equipment
Oil testing for transformers involves various analytical techniques and specialized equipment, including:
- Dissolved Gas Analysis (DGA):Measures dissolved gas concentrations in the oil, providing insights into potential issues like overheating, partial discharges, or arcing.
- Dielectric Breakdown Voltage Testing: Assesses the oil’s ability to withstand electrical stress, a key indicator of its insulating performance.
- Interfacial Tension (IFT) Measurement:Evaluates the oil’s stability at the water interface, with changes indicating contamination or oxidation.
- Fourier Transform Infrared (FTIR) Spectroscopy: Identifies the chemical composition of transformer oil, including the presence of additives, contaminants, and degradation by-products.
How to Interpret Oil Testing Results
Interpreting oil testing results is critical for understanding the transformer’s condition and determining appropriate actions. Experienced professionals evaluate various parameters, comparing them to industry standards and historical data to identify abnormalities or trends that may indicate underlying issues.
For example, increased concentrations of dissolved gases like hydrogen or acetylene may suggest partial discharges or overheating. Similarly, a decrease in dielectric breakdown voltage or an increase in acid number may indicate the need for oil filtration or replacement.
By taking a holistic approach to interpreting oil testing data, professionals provide informed recommendations for maintenance, repairs, or replacement, ensuring reliable transformer operation.
Importance of Professional Oil Testing Services
Entrusting oil testing to professional service providers ensures the accuracy and reliability of results, as well as the effective implementation of maintenance strategies. Professional services offered:
- Accurate and Reliable Results:Calibrated equipment and strict quality control protocols ensure accurate and reliable oil testing results.
- Comprehensive Analysis and Interpretation:In-depth analysis and interpretation of data, identifying potential issues, and recommending corrective actions.
- Compliance with Industry Standards:Adherence to ASTM (American Society for Testing and Materials) standards ensures quality testing procedures and reporting.
- Customized Maintenance Strategies:Tailored maintenance strategies based on the specific needs and conditions of the transformer.
Conclusion
In the world of electrical power systems, the importance of oil testing for transformers cannot be overstated. As the backbone of modern power grids, transformers play a crucial role in delivering reliable electricity. Oil testing provides invaluable insights into the condition of a transformer’s insulating oil, enabling early detection of potential issues and facilitating timely maintenance actions.
The benefits of regular oil testing include improved reliability, extended lifespan, and significant cost savings. By embracing this essential practice, companies can unlock the power of their transformers, ensuring they remain resilient, efficient, and ready to meet the evolving energy needs of the future.