Effectively reducing the TAN Levels of 32kl of FRF Oil
Abating TAN Levels: Minimac's Tailored Solution for Critical Oil Values at India's 9th Largest Coal-Fired Power Plant
Synopsis
In Singrauli, MP, stands a colossal thermal power plant, one of the largest PSUs and the 9th largest coal-fired power station at 4760 MW capacity. Recently, it faced a formidable challenge - high TAN Levels in two 16kl control fluid tanks. To prevent a potential disruption and subsequent shutdown, Minimac provided a customized solution by deploying a specialized machine to lower TAN levels, address moisture, solid contamination and implement effective Nitrogen Blanketing.
Initial Findings
Two of the control fluid tanks had elevated levels of TAN, Moisture & NAS, which had a direct impact on the Servo Valve Operations.
Oil Values | NAS | TAN | Moisture Level |
---|---|---|---|
Control Fluid Tank at UNIT 11 | Class 8 | 0.62 mg KOH/g | 561 PPM |
Control Fluid Tank at UNIT 12 | Class 7 | 0.52 mg KOH/g | 500 PPM |
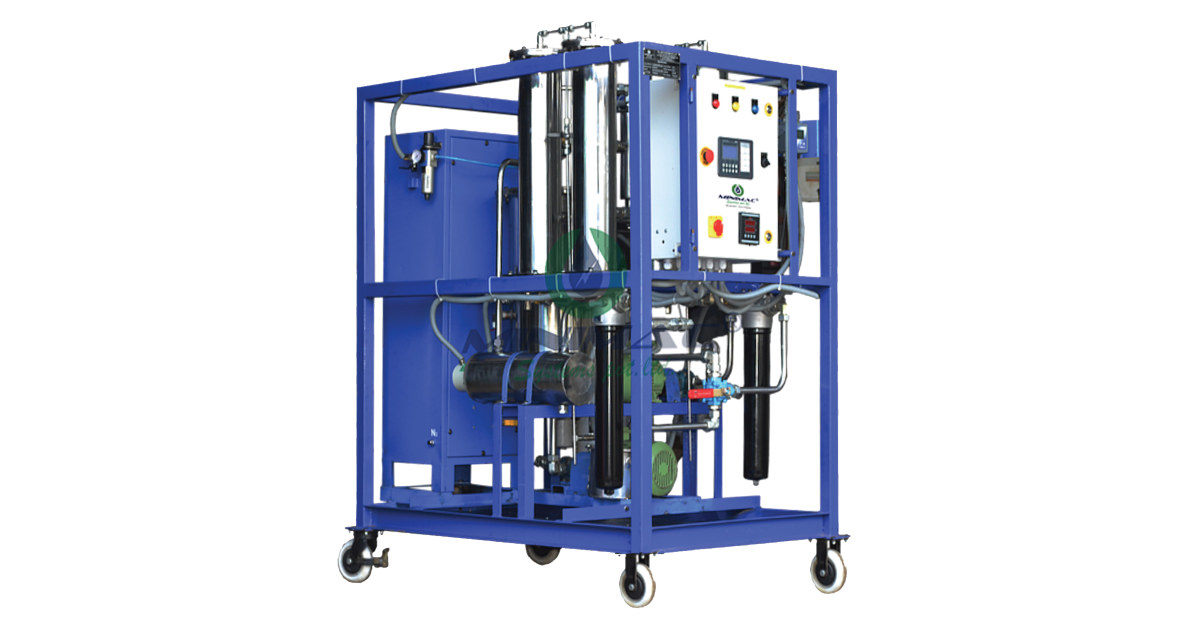
Problems
The client encountered increased TAN levels in two of their Control Fluid Tanks which had a detrimental impact on the operation of servo valves leading to reduced responsiveness, erratic behavior, increased wear and tear, and potential valve malfunction.
Client’s Requirements
- To Purify 32kl of FRF Oil
- To remove the TAN, Moisture and Solid Contaminants.
- To Achieve NAS: ≤ Class 5.
- To Achieve TAN: ≤ 0.10 (mg KOH/g).
- To Achieve Moisture: ≤ 500 ppm.
- Customized Solution.
Solutions
Deploying Minimac’s customized machine at the site along with trained and skilled engineers.
- TAN Reduction Systems(20 LPM) equipped with the ion exchange resin to filter and eliminate acid components of oil.
- Low Vacuum Dehydrator (100 LPM) to maintain consistent moisture levels in the oil using the vacuum dehydration ensuring smooth turbine operation in its active state.
- Oil filtration system(150 LPM) to bring the NAS level of oil to the desired range.
- Nitrogen blanketing system to maintain an inert space above the oil in the tank, serving as a barrier between the moisture-laden external air and the FRF oil inside the tank.
- Along with the equipment’s installation, our Service Engineer trained the client’s team on the functioning and effective handling of the machine.
- Job executed within a limited time-span on the running unit without hindering the client’s operations and control fluid tank system.
Value Type | Control Fluid Tank at UNIT 11 | Control Fluid Tank at UNIT 12 | ||
---|---|---|---|---|
Before | After | Before | After | |
NAS | Class 8 | Class 4 | Class 7 | Class 4 |
TAN | 0.62 mg KOH/g | 0.08 mg KOH/g | 0.52 mg KOH/g | 0.08 mg KOH/g |
Moisture Level | 561PPM | 275 PPM | 500 PPM | 184 PPM |
Benefits
- Prevented the environment from harm by averting the emission of 3,84,000 kg of CO2e.
- Saved 32 kl of Oil from being incinerated.
- Extended Oil Life.
- Reduced TAN Levels.
- Elimination of Oil Replacement Costs.
Cost Saving
This Plant managed to save:
Cost of Oil Replacement: ₹7 Cr. Approx.
Cost of Downtime : ₹1 Cr. Approx.
CO2e Savings
Total Savings =3,84,000 kg of CO2e/0.384 gigagrams of CO2e
Graph
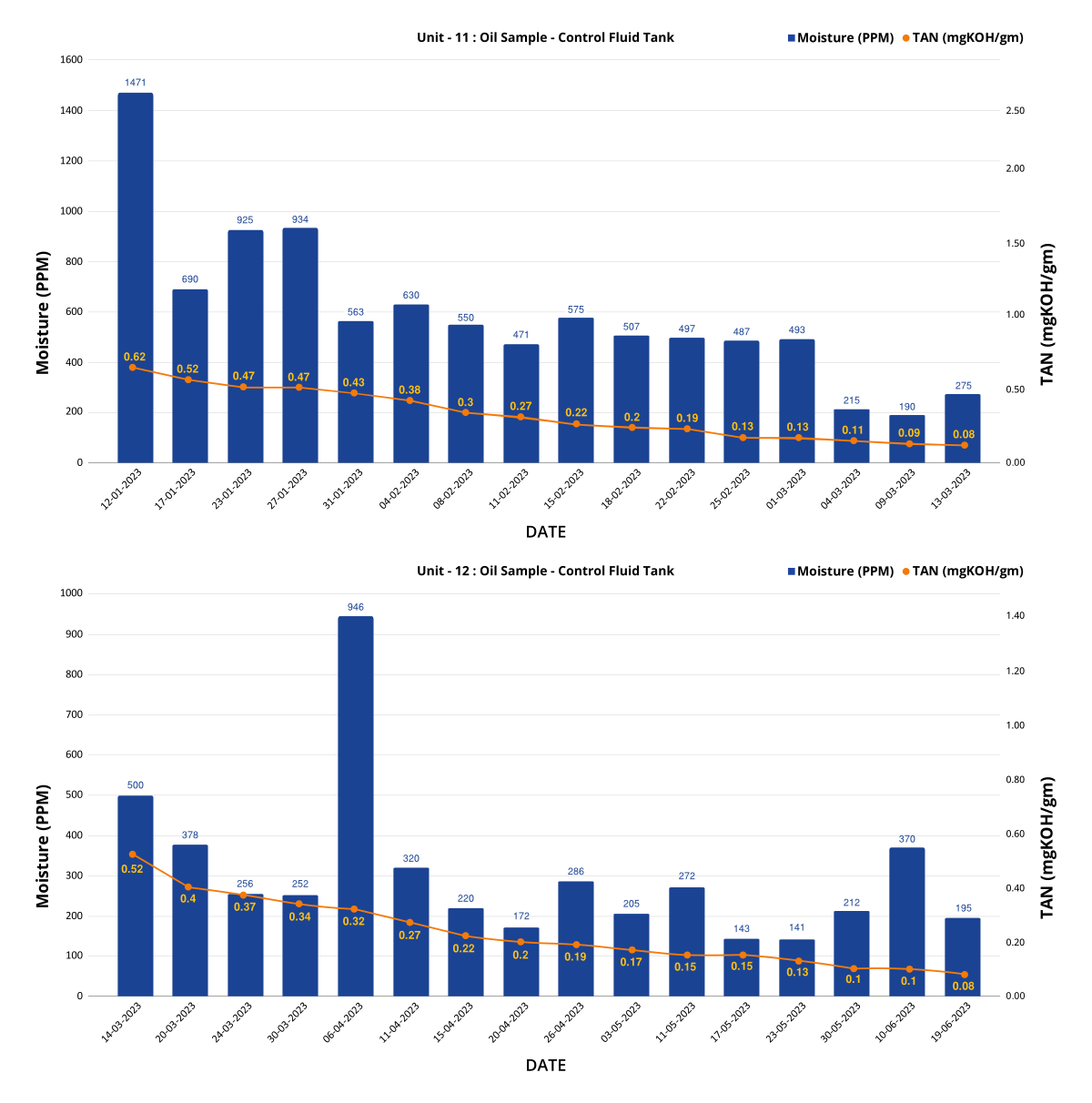
Pictorial Representation
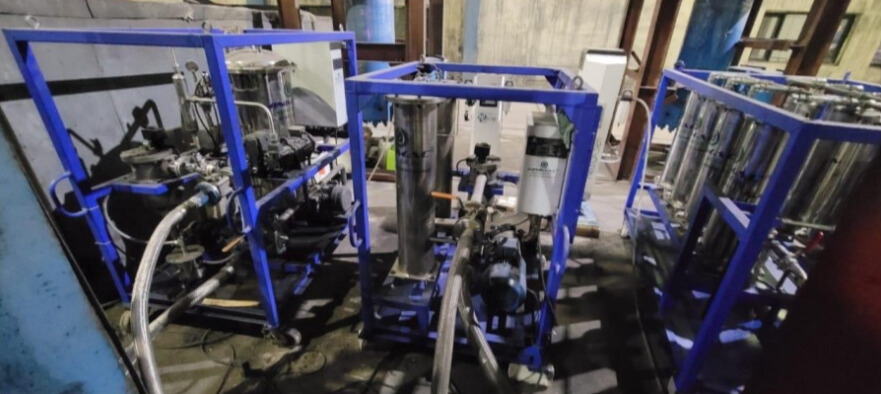
Right to left( LVDH:100LPM, FS :150LPM, TAN Reduction Skid Ion Exchange :20LPM)
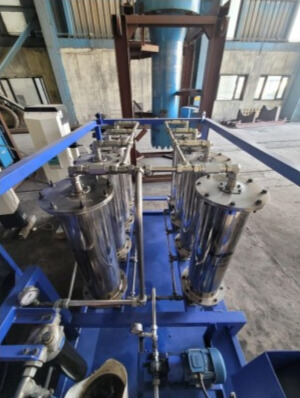
Resin Skid-TAN REDUCTION M/C (Ion Exchange 20 LPM)
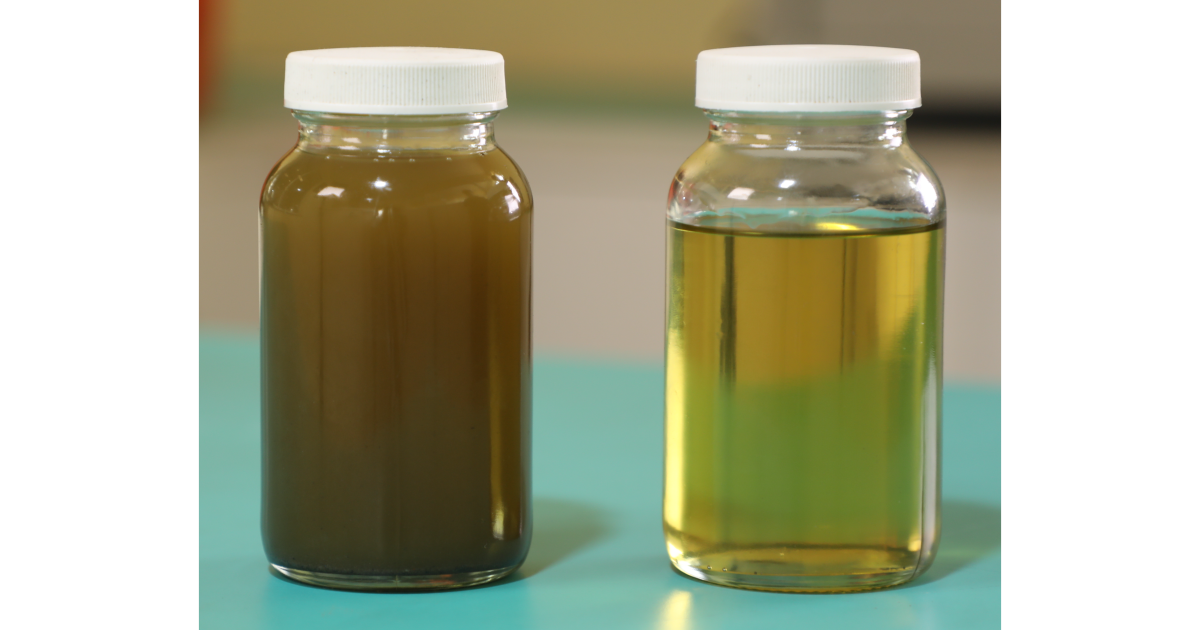
Before and after oil sample
Subscribe to our YouTube Channel and be a part of our Journey -
Click
Here