Efficiently Eliminating Varnish from 23,500 Liters of Oil in Just 516 Hours
Mitigating a Potential Power Crisis in Western India through Varnish and Solid Contamination Removal
Synopsis
A Power Plant supplying a major 1967 MW of power to the Western India, based in Dabhol, Maharashtra,and owned by one of the largest PSU’s, faced troubles with recurring turbine trip downs in two of its main turbines due to a sticky oil residue.Varnish and Solid Contaminants were identified with initial MPC values ΔE=38.6 and NAS 1638=Class 12, which needed reduction to ΔE≤15 and NAS 1638≤Class 6.Minimac's FS 500 machine, with a 3-stage system, achieved this in 516 hours, preventing frequent tripping, valve failures, erratic operations, extensive overhauls, and potential losses of ₹50 lakhs.
Initial Findings
Minimac's team conducted a site visit, analyzing the situation and taking an initial oil sample. Third-party lab testing revealed significant findings, with initial oil MPC values at ΔE=38.6 and NAS 1638 classification of Class 12.
Problems
The client encountered frequent turbine shutdowns in two of its primary turbines due to sticky oil residue within the Gas Turbines' (GTs) bearings and valves. A subsequent oil analysis confirmed the existence of varnish in the oil. As a result, Minimac was entrusted with the responsibility of removing the varnish from the main lube oil.
Client’s Requirements
- To Purify 23,500 liters of Prime 32 oil.
- To remove the varnish and solid contaminants.
- To Achieve ΔE≤15 from its initial reading of 38.6.
- To achieve NAS 1638≤Class 6 from its initial reading of Class 12.
- Smooth & Timely Execution without any downtime.
- Customized Solution.
- No spillage.
Solutions
Deploying our customized machine at the site along with our trained and skilled engineers
- FS 500: A miraculous 500-liter-per-minute machine featuring a 3-stage flushing and filtration system
- It encapsulates varnish removal capacity and mechanical filters to effectively give the desired results.
- It was connected to the main oil tank (MOT) of unit 3A, which contained 23,500 liters of Prime 32 oil.
- Along with the equipment’s installation, our Service Engineer trained the client’s team on the functioning of the machine and the effective handling of the same.
- Job executed 24/7, with continuous oil testing. Remarkably, set KPIs achieved in just 516 hours, showing significant improvement, reaching ΔE=7.2 and NAS 1638: Class 6.
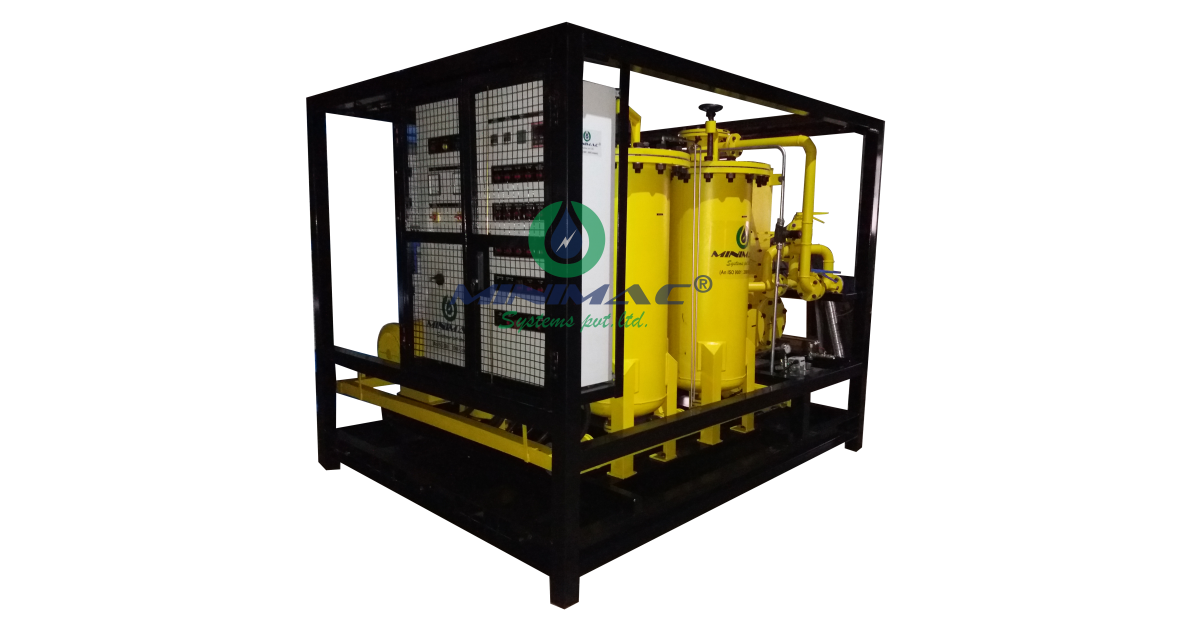
Benefits
- Prevented the environment from harm by averting the emission of 2,82,000 kilograms of CO2e.
- Extended Oil Life.
- Elimination of Oil Replacement Costs.
- An enormous quantity of oil was cleaned in a limited amount of time.
- Increased Machine Reliability.
Cost Saving
This Plant managed to save:
Cost of Oil Replacement: ₹50 Lakhs Approx.
Cost of Downtime : ₹1 Cr. Approx.
CO2e Savings
Total Savings = 2,82,000 kg of CO2e/0.282 gigagrams of CO2e
Graph
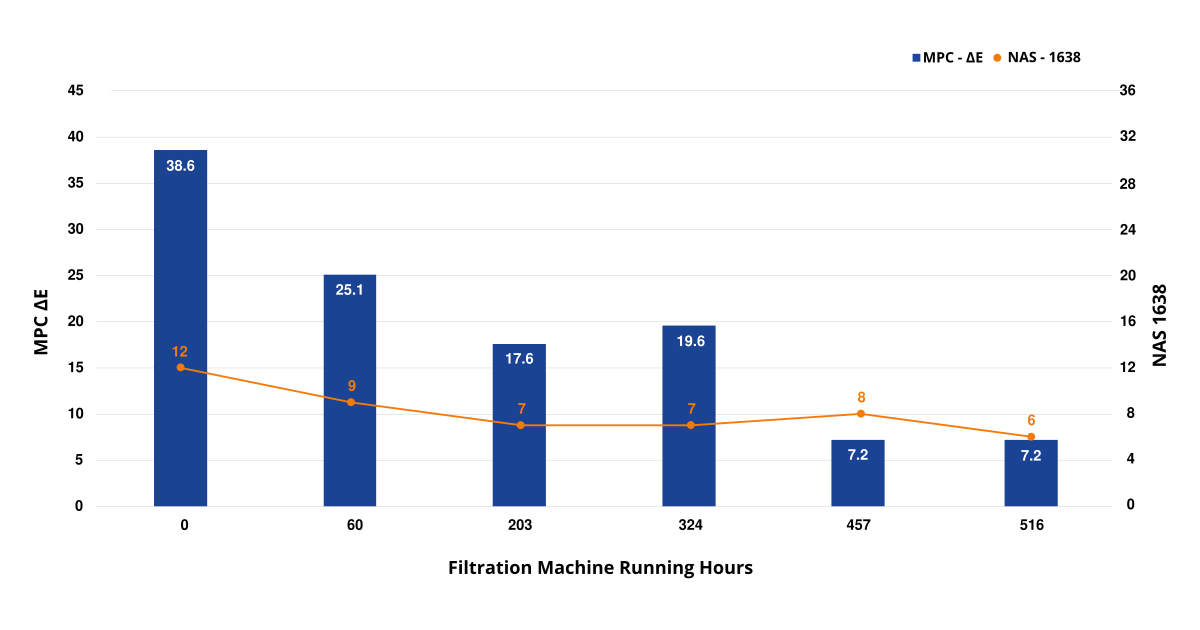
Subscribe to our YouTube Channel and be a part of our Journey - Click Here