How Flushing Solves Varnish Problems: The Essential Maintenance Solution for Reliable Equipment Performance
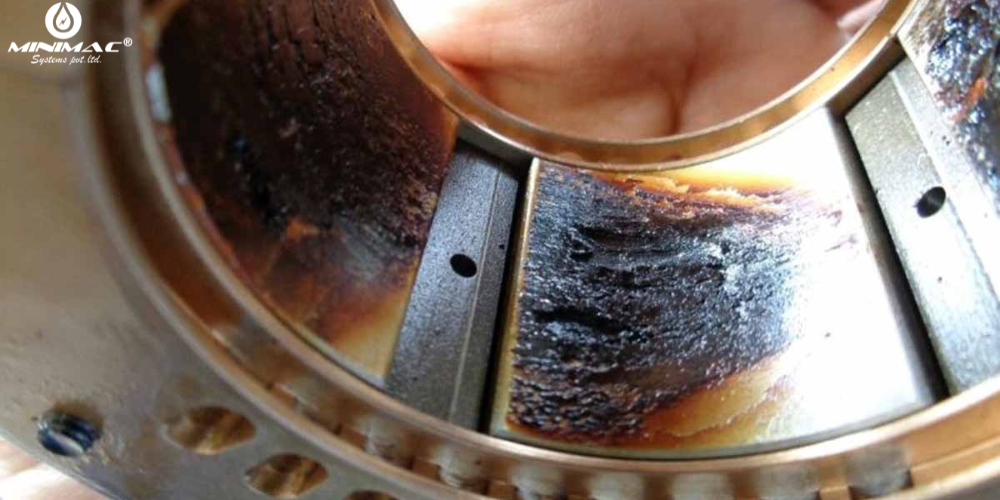
Introduction to Oil Varnish
What Is Oil Varnish?
Oil varnish is a sticky, resin-like substance that forms on surfaces within machinery. Created through the degradation of lubricants, it typically adheres to metal surfaces and can accumulate over time. Varnish creates a thin film on machine components, affecting performance and shortening machinery life.
Importance of Addressing Oil Varnish in Industrial Applications
Ignoring oil varnish can lead to operational inefficiencies, breakdowns, and higher maintenance costs. For industries with extensive machinery, such as manufacturing, power generation, and transportation, managing varnish is essential to preserving the reliability and efficiency of equipment.
The Role of Maintenance in Addressing Varnish Problems
Effective maintenance is key to minimizing varnish problems and the resulting operational issues. Preventive maintenance practices, such as regular lubricant checks, filtration, and equipment inspections, can slow down the formation of varnish but often cannot entirely prevent it. Therefore, maintenance teams are tasked with finding more proactive methods to remove varnish deposits and reduce their negative impact.
The traditional approach to cleaning varnish has involved physically scrubbing affected surfaces, which is labor-intensive, time-consuming, and often only partially effective. Fortunately, flushing presents an innovative and efficient alternative that provides deeper cleaning and superior results, making it an essential part of a robust maintenance program.
Understanding Flushing as a Solution
Flushing is the process of removing contaminants from a system by circulating a flushing fluid through it. This fluid, under high velocity or pressure, helps dislodge and remove stubborn varnish deposits from internal surfaces. Various types of flushing methods can be applied depending on the system requirements and the severity of the varnish buildup:
- High-velocity flushing:This method involves using a flushing fluid at high velocity to lift and dislodge deposits. It’s commonly used for large systems with heavy varnish buildup.
- Chemical flushingIn cases where mechanical flushing may not be enough, specialized chemical additives are introduced to dissolve varnish, making it easier to remove.
- Mechanical flushing:This involves physical scrubbing or agitation, often combined with fluid flow, to break up and remove debris.
Flushing not only eliminates varnish but also removes other contaminants that may contribute to equipment degradation.
How Flushing Removes Varnish Deposits
Flushing is effective in removing varnish because it uses a combination of fluid pressure, chemical action, and sometimes mechanical agitation to target deposits. The flushing process typically involves the following steps:
- PreparationThe system is drained of existing lubricant, and flushing fluid is introduced.
- Circulation:The flushing fluid is circulated at a high velocity, which helps loosen varnish and other deposits from system surfaces.
- Filtration: The fluid is filtered continuously during the flushing process, removing suspended particles.
- Inspection: After a thorough flush, the system is inspected to ensure all varnish has been removed, and a new lubricant is introduced.
Compared to traditional cleaning, flushing is far more comprehensive, often reaching areas that are inaccessible through manual methods. Additionally, flushing can be performed with minimal disassembly, reducing the time and labor involved.
Types of Equipment and Systems That Benefit from Flushing
Varnish can affect a range of industrial systems, and flushing can be applied to various equipment types to remove these deposits effectively. Some common applications include:
- Hydraulic systems:Varnish in hydraulic systems can cause valves to stick, reducing system responsiveness and efficiency.
- Turbines: Varnish can interfere with turbine bearings and lubrication pathways, affecting performance and increasing the risk of failure.
- Compressors: Varnish deposits can impair heat transfer and lubrication in compressors, leading to reduced efficiency and overheating.
Flushing is particularly useful for these systems because it can thoroughly clean components without requiring major disassembly, saving both time and money.
Benefits of Flushing for Maintenance and Operations
Flushing provides several significant benefits for maintenance teams, particularly in the context of varnish removal:
- Improved Efficiency:By removing varnish, flushing helps restore system performance, ensuring components function as designed.
- Extended Equipment LifeFlushing prevents varnish buildup from damaging parts, thereby prolonging the equipment's lifespan.
- Reduced Downtime:As flushing is more effective and quicker than manual cleaning, it minimizes equipment downtime, allowing operations to resume swiftly.
- Cost Savings:Fewer repairs and less frequent maintenance mean significant cost savings for the organization.
For maintenance teams, these benefits make flushing an invaluable addition to their toolkit, particularly when managing high-performance equipment in challenging environments.
Best Practices for Effective Flushing
To get the best results from flushing, it’s essential to follow certain best practices:
- Selecting the Right Flushing Method:Depending on the severity of varnish buildup, choose between high-velocity, chemical, or mechanical flushing.
- Timing and Frequency:Flushing should be performed at intervals that prevent varnish from accumulating to critical levels.
- Safety and Environmental Considerations:Ensure that the flushing fluid used is safe for the environment and compatible with the equipment material.
Using these best practices helps maintenance teams maximize the effectiveness of flushing and reduce varnish problems across the board.
Subscribe to our website blog for more technical articles and case studies: Click here
Flushing in a Comprehensive Varnish Management Strategy
While flushing is a powerful tool, it should be part of a broader varnish management strategy. This strategy might include:
- Regular Monitoring:Monitoring varnish levels through oil analysis can help identify buildup before it becomes a problem.
- Improved Filtration Systems:Installing high-quality filters can reduce the contaminants that contribute to varnish formation.
- Routine Fluid Replacement:Using fresh lubricants or oils with high oxidation stability can slow down varnish formation.
Integrating flushing with these preventive measures provides a complete approach to varnish control, ensuring that machinery remains in peak condition
Conclusion:
Flushing stands out as an effective, reliable, and efficient solution to varnish problems in industrial settings. By addressing varnish buildup proactively, maintenance teams can improve equipment efficiency, reduce costs, and extend the life of critical machinery. For industries relying on high-performance equipment, investing in regular flushing is a smart move that enhances both operational reliability and profitability.
As companies continue to prioritize equipment maintenance and longevity, flushing will play an increasingly important role in comprehensive varnish control strategies.
FAQS:
Q. What is oil varnish?
A: Oil varnish is a sticky, resin-like substance that forms on the surfaces inside industrial machinery due to the degradation of lubricants. This varnish builds up over time and can negatively affect the performance of machinery by coating components like valves, pumps, and bearings, impeding their function.
Q. What is the function of varnish?
A: In general, varnish serves as a protective coating for surfaces. However, in machinery, varnish is an unwanted byproduct of oil degradation and does not serve a beneficial function. Instead, it can impede smooth operation by causing clogging, increasing friction, and reducing heat transfer.
Q. How is varnish formed?
A: Varnish is primarily formed through the thermal degradation of lubricants in high-temperature environments. The breakdown of oil molecules leads to the creation of insoluble compounds. These compounds can build up over time, particularly when oxidized oil reacts with contaminants like dirt, water, and metal particles, accelerating the varnish formation process.
Q. How do you maintain varnish?
A: Maintaining varnish involves early detection and management to prevent excessive buildup. Routine oil monitoring, using quality lubricants, and applying preventive maintenance practices like oil flushing and filtration systems are effective ways to control and manage varnish formation.
Q. What causes oil varnish?
A: The primary causes of oil varnish include:
- Thermal degradation: High temperatures break down oil molecules.
- Oxidation: Oxygen reacts with oil, forming harmful compounds.
- Contaminants: Dirt, water, and metal particles can accelerate the varnish formation process.
- Hydraulic stress and pressure: These factors can also cause oil degradation, promoting varnish buildup.
Q. What are the advantages of flushing?
A: Flushing has several advantages in managing varnish:
- Removes contaminants: It cleans the system by removing varnish particles, dirt, and other contaminants.
- Restores oil flow: Flushing helps restore the efficiency of the lubrication system by clearing blockages.
- Prevents further damage: It minimizes wear and tear on machinery components.
- Improves overall performance: By maintaining cleaner oil, flushing ensures optimal lubrication and cooling.
Q. What is flushing in maintenance?
A: Flushing in maintenance refers to the process of circulating a cleaning fluid or solvent through a system to remove contaminants like varnish, debris, and oxidation products from the internal surfaces of machinery. It's an essential procedure to ensure the system operates efficiently and to extend the equipment's lifespan.
Q. What is the purpose of the flushing system?
A: The purpose of a flushing system is to ensure that machinery remains clean and free of harmful contaminants. The system circulates fluid through the equipment to flush out accumulated varnish, particles, and degradation products, improving efficiency and preventing breakdowns.