Low Oil Pressure: The Hidden Dangers Lurking in Your Machine
Introduction
Oil pressure is a critical aspect of any machine’s performance, whether it’s an automobile, industrial equipment, or any mechanical system. It plays a vital role in ensuring that all moving parts are properly lubricated, minimizing friction and preventing overheating. However, when oil pressure drops below optimal levels, it can lead to catastrophic consequences. This article aims to illuminate the hidden dangers associated with low oil pressure, helping you understand how to identify potential issues and address them before they escalate into costly repairs or even safety hazards.
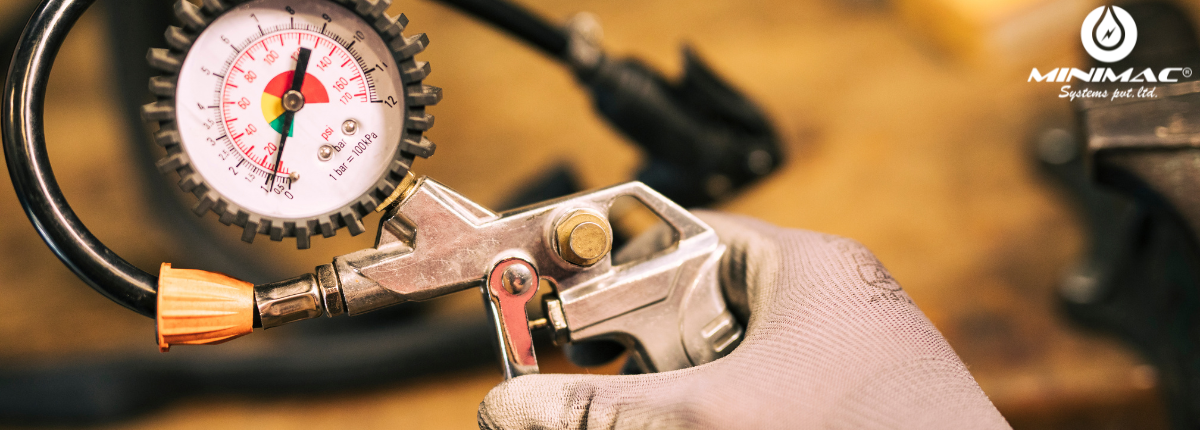
Understanding Oil Pressure
A. What is Oil Pressure?
Oil pressure refers to the force exerted by oil within a machine's lubrication system. It is essential for delivering oil to various moving parts, which helps reduce friction and wear. The oil also absorbs heat from the machine, maintaining an optimal operating temperature. If oil pressure is too low, it can compromise these functions, leading to severe mechanical issues.
B. How Oil Pressure is Measured
Oil pressure is typically measured using an oil pressure gauge. In machines, this gauge is usually located on the dashboard or control panel and displays the current oil pressure in real time. Normal oil pressure readings vary depending on the machinery type, but generally, the pressure should fall within a specific range (often between 20-60 psi for most engines). Deviations from this range can indicate potential problems, signaling the need for immediate attention.
Causes of Low Oil Pressure
Understanding the common causes of low oil pressure can help prevent potential issues before they become serious.
A. Insufficient Oil Levels
One of the most straightforward causes of low oil pressure is insufficient oil in the system. This can happen due to:
- Regular Consumption:Regular Consumption: Machines consume oil over time, especially if they are older or not maintained well.
- Leaks:Oil leaks can occur at gaskets, seals, or other points, leading to reduced oil levels.
- Neglected Maintenance:Failing to perform regular oil checks and changes can lead to low levels of oil.
B. Oil Pump Failure
The oil pump is responsible for circulating oil throughout the machine. If the oil pump fails or becomes less efficient, it can result in inadequate oil flow. Common reasons for oil pump failure include wear and tear, blockage from contaminants, or failure of the pump’s internal components.
C. Oil Leaks
Oil leaks are a common cause of low oil pressure and can occur in various locations within the machine, including:
- Gaskets:Seals between different machine components can wear out over time, leading to leaks.
- Oil Filters:Improperly installed or defective filters can leak oil.
- Hoses:Cracked or damaged hoses can also lead to oil loss.
D. Clogged Oil Filters
Oil filters are designed to remove contaminants from the oil to keep the lubrication system clean. Over time, filters can become clogged with debris, dirt, and sludge. A clogged oil filter can restrict oil flow, resulting in low oil pressure. Regularly replacing the oil filter during maintenance can help prevent this issue.
E. Worn Machine Components
As machines age, components such as bearings, piston rings, and seals can wear out. This wear can create gaps that allow oil to escape or reduce the overall efficiency of the lubrication system, leading to lower oil pressure. Regular inspections and maintenance can help identify worn parts before they cause significant damage.
Hidden Dangers of Low Oil Pressure
A. Machine Damage
Low oil pressure can lead to serious machine damage, such as:
- Seized Bearings:When bearings do not receive adequate lubrication, they can seize, leading to catastrophic machine failure.
- Scored Cylinder Walls:Insufficient lubrication can result in metal-to-metal contact, scoring the cylinder walls and leading to costly repairs.
B. Increased Wear and Tear
Inadequate lubrication increases friction among moving parts, which accelerates wear and tear. This not only shortens the lifespan of components but also leads to frequent breakdowns and costly repairs.
C. Overheating
Oil plays a significant role in cooling the machine. Low oil pressure often results in insufficient oil circulation, causing the machine to overheat. Overheating can warp machine components, damage gaskets, and lead to total machine failure.
D. Reduced Efficiency
Machines operating with low oil pressure tend to experience decreased performance. They may consume more fuel or energy, leading to increased operational costs and reduced productivity. This inefficiency can severely impact the overall cost-effectiveness of operations.
E. Safety Hazards
In industrial settings, low oil pressure can pose significant safety hazards. Machinery failures can lead to accidents, injuries, or even fatalities. Ensuring proper oil pressure is not just about maintenance; it's about creating a safe working environment.
Signs of Low Oil Pressure
A. Dashboard Warning Lights
Most modern machines are equipped with warning lights that alert operators to low oil pressure. Ignoring these warnings can lead to serious machine damage. If you see this light, it’s crucial to check your oil levels and address the issue immediately.
B. Unusual Machine Noises
If you hear knocking or grinding noises coming from the machine, it could indicate low oil pressure. These sounds suggest that metal parts are not adequately lubricated, leading to increased wear and potential damage.
C. Performance Issues
A sudden decrease in machine performance such as loss of power or acceleration can be a sign of low oil pressure. If you notice these changes, it's essential to check your oil pressure and levels as soon as possible.
How to Address Low Oil Pressure
A. Regular Maintenance
Routine maintenance is vital for preventing low oil pressure. This includes:
- Regular Oil Checks:Ensure oil levels are within the recommended range.
- Timely Oil Changes:Change the oil according to the manufacturer's recommendations to keep the lubrication system functioning optimally.
B. Monitoring Systems
Implementing monitoring systems that provide real-time readings of oil pressure can help you identify issues before they escalate. Many modern machines come equipped with advanced monitoring technology that alerts operators to potential problems.
C. Professional Inspections
If you suspect low oil pressure, it’s wise to consult a professional mechanic or technician. They can diagnose the issue accurately and recommend the best course of action.
D. Prompt Repairs
Address any identified issues immediately. Whether it involves topping off oil, replacing a faulty pump, or fixing leaks, timely action can save you from costly repairs down the line.
Conclusion
Understanding the implications of low oil pressure is crucial for anyone operating machinery. From machine damage to safety hazards, the dangers are real and can be costly. By staying vigilant and proactive about monitoring and maintaining oil pressure, you can protect your investment and ensure the smooth operation of your machines.
FAQS:
Q. What is oil pressure, and why is it important in machinery?
Oil pressure is the force exerted by oil within a machine’s lubrication system. It ensures moving parts are well-lubricated, reducing friction, wear, and heat buildup, which is vital for optimal machine performance
Q. What are the common causes of low oil pressure?
A: Common causes include insufficient oil levels, oil pump failure, oil leaks, clogged oil filters, and worn machine components, each of which can impact lubrication and machine function.
Q. How can I tell if my machine has low oil pressure?
A: Signs of low oil pressure include dashboard warning lights, unusual noises like knocking or grinding, and performance issues such as loss of power or acceleration.
Q. Can low oil pressure damage my machine?
A: Yes, low oil pressure can cause serious damage, including seized bearings, scored cylinder walls, and overheating, leading to costly repairs and a shortened machine lifespan.
Q. How often should I check my machine's oil pressure?
A: Regularly, as part of routine maintenance. Checking oil pressure often and monitoring levels can prevent issues before they become serious.
Q. What should I do if I experience low oil pressure?
A: Immediately check oil levels, inspect for visible leaks, and consider consulting a professional technician to diagnose the cause and take corrective action.
Q. How does low oil pressure affect machine safety?
A: In industrial settings, low oil pressure can lead to machinery failures, increasing the risk of accidents, injuries, or fatalities, emphasizing the importance of proper maintenance.
Q. Can clogged oil filters cause low oil pressure?
A: Yes, clogged oil filters restrict oil flow, which can result in low oil pressure. Regular filter replacement helps maintain proper oil flow and pressure.
Q. What role does the oil pump play in maintaining oil pressure?
The oil pump circulates oil throughout the system, ensuring parts are lubricated. If the pump fails or is inefficient, it can lead to low oil pressure and inadequate lubrication.
Q. How can monitoring systems help prevent low oil pressure?
A: Monitoring systems provide real-time readings of oil pressure, alerting operators to potential issues early on, and enabling quick action to prevent damage.