Maximizing Equipment Reliability with Oil Analysis and Predictive Maintenance
Introduction
In the world of machinery and equipment, the significance of oil cannot be overstated. It serves as a lubricant, reducing friction and wear between moving parts, and also plays a critical role in cooling and cleaning. However, as oil ages, it can become contaminated, leading to increased wear and potential equipment failure. This is where oil analysis comes into play. By analyzing oil samples, maintenance teams can gain valuable insights into the condition of the oil and the machinery it lubricates, enabling them to make informed decisions that prolong equipment life and enhance operational efficiency.
Understanding Oil Analysis
Oil analysis is the process of collecting samples of lubricating oil from equipment and testing them for various properties and contaminants. It provides a comprehensive view of the oil's condition and the health of the machinery. This process typically involves physical, chemical, and microscopic analysis, helping to identify contaminants such as dirt, water, and metal wear particles.
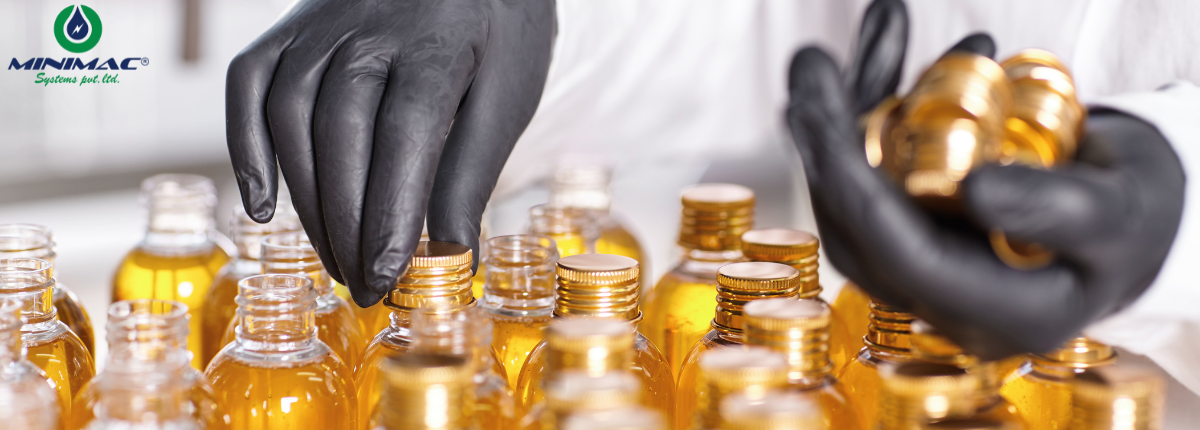
Importance of Oil Analysis
The importance of oil analysis lies in its ability to prevent costly equipment failures and extend the lifespan of machinery. Regular oil analysis can lead to:
- Reduced Maintenance Costs: By identifying potential issues early, companies can address them before they escalate, reducing the need for expensive repairs and downtime.
- Enhanced Equipment Reliability:Consistent monitoring allows for timely interventions, ensuring machinery operates at optimal efficiency.
- Improved Safety:By maintaining equipment health, organizations can minimize safety risks associated with equipment failures.
Oil Analysis Testing for Cleanliness
Oil cleanliness is crucial for maintaining the performance and reliability of machinery. Contaminants such as dirt, metal particles, and water can lead to accelerated wear and system failures. Oil analysis testing for cleanliness involves:
- Particle Counting:This method quantifies the number and size of particles in the oil, providing a clear picture of its cleanliness.
- Spectrometric Analysis:This technique detects and quantifies metal wear particles, helping to identify specific sources of contamination and wear.
Oil Analysis for Clean Oil
To ensure the machinery operates smoothly, it is essential to maintain clean oil. Oil analysis helps in this regard by:
- Identifying Contaminants:Regular analysis can detect the presence of harmful substances before they cause damage.
- Determining Oil Life:nalysis helps assess whether the oil is still effective or needs to be changed, preventing unnecessary oil waste.
Oil Condition Monitoring
Oil condition monitoring is a proactive approach to maintenance that involves regularly testing oil samples to monitor their condition. This practice can help:
- Identify Changes Over Time: By tracking the condition of the oil, maintenance teams can spot trends that indicate wear or contamination.
- Establish Oil Change Intervals:Regular monitoring helps in determining the most effective intervals for oil changes based on actual oil conditions rather than arbitrary schedules.
Clean Oil Analysis
Clean oil analysis focuses on determining the purity and effectiveness of the oil in use. Key aspects include:
- Viscosity Testing: This tests the oil's thickness and flow characteristics, essential for proper lubrication.
- Oxidation Measurement:Oxidation can lead to the formation of sludge and varnish, negatively impacting oil performance. Analyzing oxidation levels helps in assessing oil health.
Predictive Oil Analysis
Predictive oil analysis takes oil testing a step further by using data analytics and trends to forecast potential issues. This includes:
- Data Correlation:By correlating oil analysis data with equipment performance metrics, predictive analysis can help anticipate when maintenance should occur.
- Machine Learning Algorithms:Advanced technologies can analyze historical data to predict future failures, allowing for more strategic maintenance planning.
How Oil Analysis Helps Maintain Clean Oil
Oil analysis plays a crucial role in maintaining clean oil through several mechanisms:
- Regular Monitoring:Frequent analysis ensures that any contaminants are detected early, allowing for timely action.
- Feedback Loop:Analysis results create a feedback loop that informs maintenance strategies and adjustments.
- Cost-Effectiveness:By preventing contamination and extending oil life, oil analysis can lead to significant savings over time.
Tips to Consider When Doing Oil Analysis
- Choose the Right Testing Laboratory:Ensure that the lab has a good reputation and uses industry-standard testing methods.
- Standardize Sampling Procedures:Consistent sampling methods lead to more reliable and comparable results.
- Maintain a Regular Schedule:Develop a routine for oil analysis to catch potential problems early.
- Educate Your Team:Ensure that all personnel involved in sampling and analysis understand the importance of the process.
- Use the Right Equipment: Ensure that sampling tools and containers are clean and appropriate for the type of oil being analyzed.
Innovations in Oil Filtration
Recent innovations in oil filtration technology have significantly enhanced oil analysis processes. These include:
- Advanced Filtration SystemsNew filtration technologies can remove smaller particles and contaminants more efficiently.
- Real-Time Monitoring:IoT-enabled devices can provide continuous oil condition monitoring, alerting maintenance teams to issues as they arise.
- Smart Analytics:Machine learning algorithms analyze oil data, predicting potential issues before they become critical.
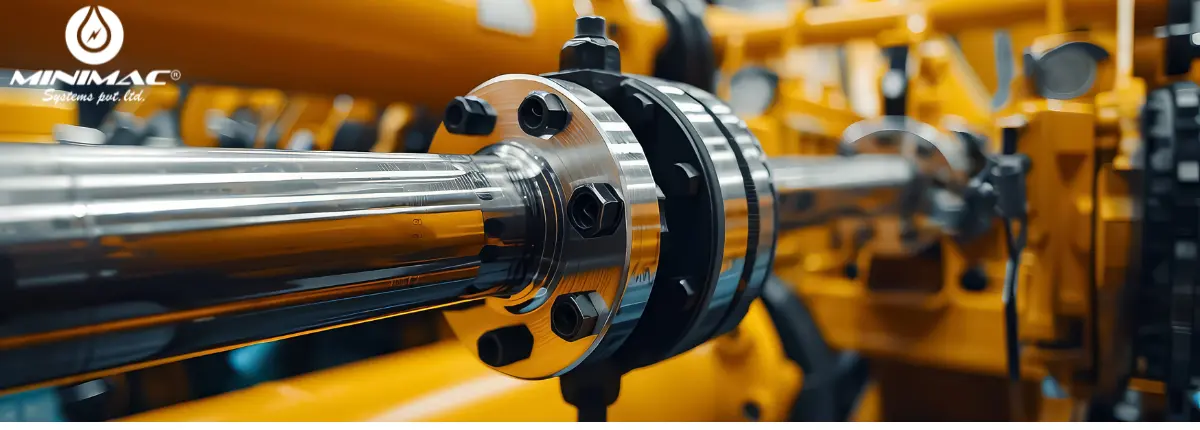
Benefits of Oil Analysis
Oil analysis offers numerous benefits that are essential for maintaining equipment reliability and optimizing operational efficiency. Here are some of the key advantages:
- Early Detection of Problems:Oil analysis helps identify potential issues before they escalate into significant failures. By detecting contaminants or abnormal wear patterns early, maintenance teams can address problems proactively.
- Cost Savings:By preventing costly repairs and unplanned downtime, regular oil analysis can lead to significant cost savings. Identifying issues early allows for more targeted maintenance strategies, reducing overall maintenance expenses.
- Extended Equipment Life: Consistent monitoring and analysis of oil conditions help prolong the life of machinery. By ensuring that equipment runs on clean, effective oil, organizations can minimize wear and tear.
- Improved Reliability: Regular oil analysis enhances equipment reliability by maintaining optimal lubrication conditions. This reduces the likelihood of breakdowns and operational interruptions.
- Optimized Maintenance Schedules:Oil analysis provides data-driven insights that allow organizations to optimize maintenance schedules. Instead of following arbitrary timelines for oil changes, companies can change oil based on actual condition and performance data.
- Increased Operational Efficiency:Clean and well-maintained oil contributes to improved machine efficiency, enhancing overall productivity. This can lead to better output and reduced energy consumption.
- Enhanced Safety:By maintaining equipment health through oil analysis, organizations can reduce the risk of equipment failures that may pose safety hazards to personnel.
- Better Understanding of Equipment Health:Oil analysis provides a comprehensive view of the overall health of machinery. It allows maintenance teams to track trends over time, making it easier to assess equipment performance and anticipate future issues.
- Environmental Benefits: Regular oil analysis can lead to reduced oil waste by optimizing oil usage and extending its life. This contributes to more sustainable operations and minimizes environmental impact.
- Data-Driven Decision Making: Oil analysis provides valuable data that supports informed decision-making regarding maintenance strategies, oil purchasing, and equipment upgrades.
- Predictive Maintenance Opportunities: By incorporating oil analysis into a predictive maintenance program, organizations can forecast potential failures based on data trends, allowing for proactive interventions and reducing the likelihood of unexpected downtime.
- mpliance with Industry Standards: Regular oil analysis helps organizations adhere to industry regulations and standards regarding equipment maintenance and performance, ensuring compliance and enhancing reputation.
- Customized Maintenance Strategies:Analysis results can lead to tailored maintenance strategies specific to each piece of equipment or operational context, ensuring that resources are allocated efficiently.
Overall, oil analysis serves as a crucial tool in modern maintenance practices, enabling organizations to enhance equipment reliability, optimize operational performance, and achieve significant cost savings.
Conclusion
Oil analysis is an essential practice for maintaining equipment reliability and efficiency. By understanding its importance and implementing regular oil analysis programs, organizations can prevent costly failures, extend machinery life, and ensure optimal performance. With advancements in oil filtration and predictive technologies, the future of oil analysis looks promising, providing further opportunities for enhancing operational excellence.
FAQS:
What is oil analysis?
A: Oil analysis is the process of testing lubricating oil for contaminants and properties to assess its condition and the health of machinery.
Why is oil analysis important?
A: It helps prevent equipment failures, reduce maintenance costs, and extend the lifespan of machinery.
Q: What contaminants can oil analysis detect?
A: Oil analysis can identify dirt, water, metal wear particles, and oxidation by-products.
Q: How often should I perform oil analysis?
A: It is advisable to conduct oil analysis regularly, depending on the equipment's operating conditions and manufacturer recommendations.
Q: What is predictive oil analysis?
A: Predictive oil analysis uses data analytics to forecast potential equipment failures based on oil condition trends.
Q: How can I ensure clean oil?
A: Regular oil analysis, proper storage, and effective filtration systems can help maintain clean oil.
Q: What are the benefits of clean oil analysis?
A: Clean oil analysis helps in identifying oil purity and effectiveness, ensuring optimal machinery performance.
Q: What role does oil viscosity play in oil analysis?
A: Viscosity testing determines the oil's flow characteristics, which are critical for effective lubrication.
Q: Can oil analysis prevent equipment failures?
A: Yes, by identifying issues early, oil analysis allows for timely maintenance actions that can prevent failures.
Q: What innovations are currently improving oil filtration?
A: Innovations include advanced filtration systems, real-time monitoring technology, and smart analytics for predictive maintenance.
Click here to learn more about oil condition monitoring equipment - Click here