Unlocking the Power of Oil Filtration: A Deep Dive into Maximizing Efficiency and Extending Equipment Lifespan
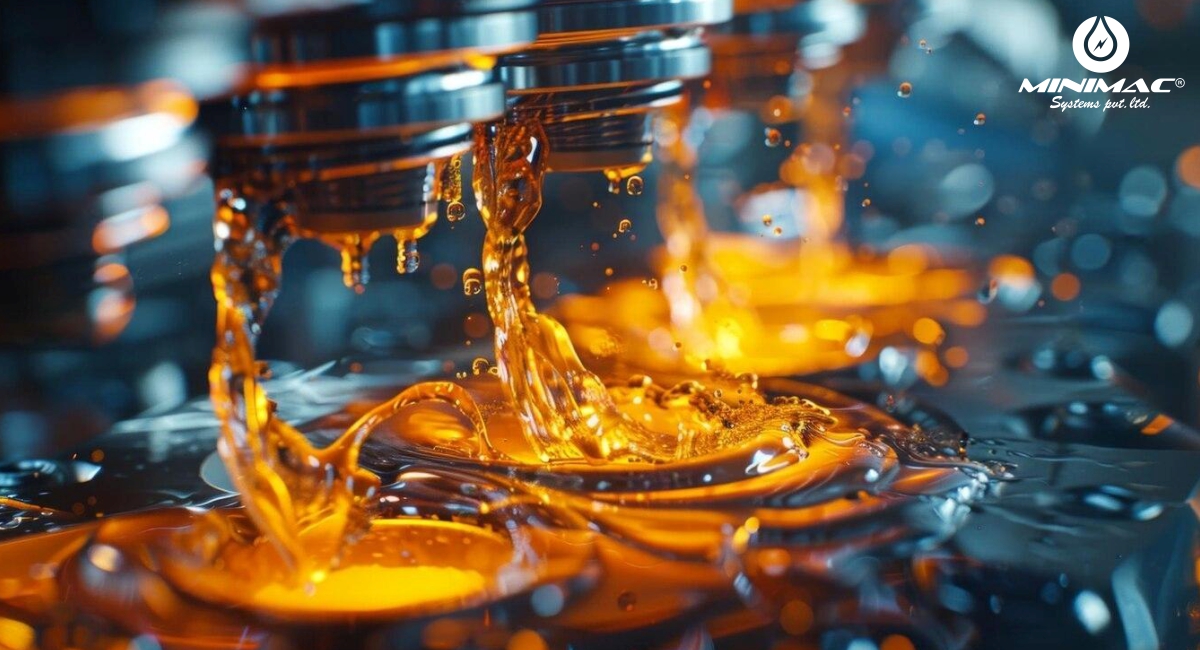
Introduction
Oil filtration is a critical process that ensures the optimal performance and longevity of machinery that relies on lubricating oil. By effectively removing contaminants and impurities, oil filtration systems play a pivotal role in preventing costly breakdowns, reducing downtime, and enhancing overall equipment efficiency. This comprehensive guide will delve into the intricacies of oil filtration, exploring its significance, mechanisms, benefits, different types of oil filters, and best practices for maximizing its effectiveness.
Understanding the Importance of Oil Filtration:
Oil filtration is essential for maintaining the health of machinery. Without proper filtration, harmful substances like dirt, metal shavings, and water can circulate through the system, accelerating wear and tear on vital components. This leads to decreased equipment life, increased maintenance costs, and potential catastrophic failures.
By investing in a robust oil filtration system, you can significantly extend the lifespan of your equipment, improve its performance, and reduce operational costs. Clean oil ensures optimal lubrication, reducing friction, lowering operating temperatures, and enhancing energy efficiency.
How Does Oil Filtration Work?
Oil filtration involves removing contaminants from lubricating oil. The oil is drawn from the machinery, passes through a filter element to capture impurities, and is then recirculated back into the system. The filter element, typically made of paper, synthetic fibers, or metal screens, is the heart of the filtration process.
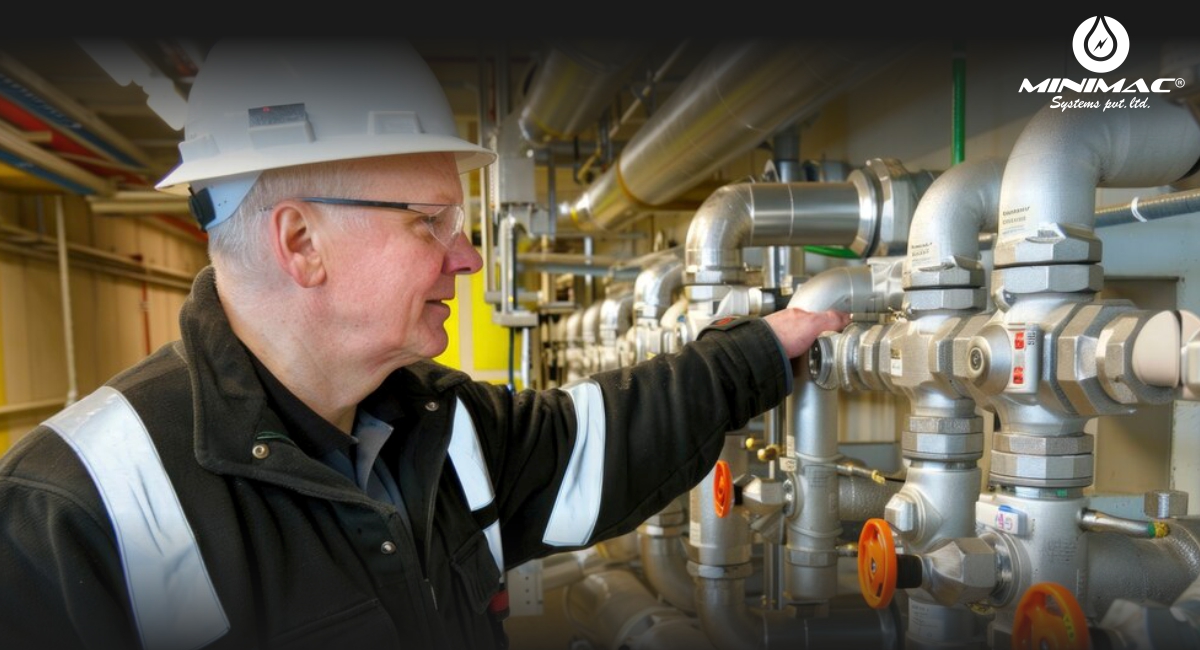
Benefits of Oil Filtration
- Extended Equipment Lifespan: Reduces wear and tear on critical components.
- Improved Efficiency and Performance: Ensures optimal lubrication, reducing friction and energy consumption.
- Reduced Maintenance and Downtime: Minimizes the frequency of oil changes and component replacements.
- Cost Savings: Prevents costly repairs and replacements, leading to significant financial benefits.
Types of Oil Filters
There are several types of oil filters, each designed to address specific filtration needs:
- Spin-on Filters: Easy to install and replace, featuring a replaceable cartridge housed in a metal canister.
- In-line Filters: Installed directly into the oil flow path, suitable for space-constrained applications.
- Magnetic Oil Filters: Utilize powerful magnets to capture ferrous metal particles, which are ideal for high contamination risk environments.
Choosing the Right Oil Filtration System
Selecting the appropriate oil filtration system requires considering the following:
- Oil Flow Rate: Ensure the filter can handle the oil volume circulating through your machinery.
- Contaminant Type and Size: Choose a filter capable of capturing the specific contaminants present in your system.
- Oil Compatibility: Verify that the filter is compatible with the oil type used in your equipment.
Deep Dive: Filter Media - The Heart of Oil Filtration
The choice of filter media is crucial for effective oil filtration. Different types of filter media have varying capabilities in capturing contaminants.
- Paper Filter Media: Commonly used for general-purpose filtration, offering good dirt-holding capacity.
- Synthetic Fiber Filter Media: Provides higher dirt-holding capacity and longer service life compared to paper media.
- Metal Mesh Filter Media: Ideal for removing larger contaminants, often used as a pre-filter.
- Activated Carbon Filter Media: Used to remove impurities like water and organic contaminants.
Oil Filtration System Design Considerations
Designing an efficient oil filtration system involves several factors:
- Filter Placement: Consider the optimal location of the filter in the oil circuit for maximum efficiency.
- Bypass Valve: Incorporate a bypass valve to prevent excessive pressure buildup and protect the system
- Differential Pressure Gauge: Monitor pressure drop across the filter to indicate filter condition.
- Filter Housing Material: Choose a corrosion-resistant material for the filter housing.
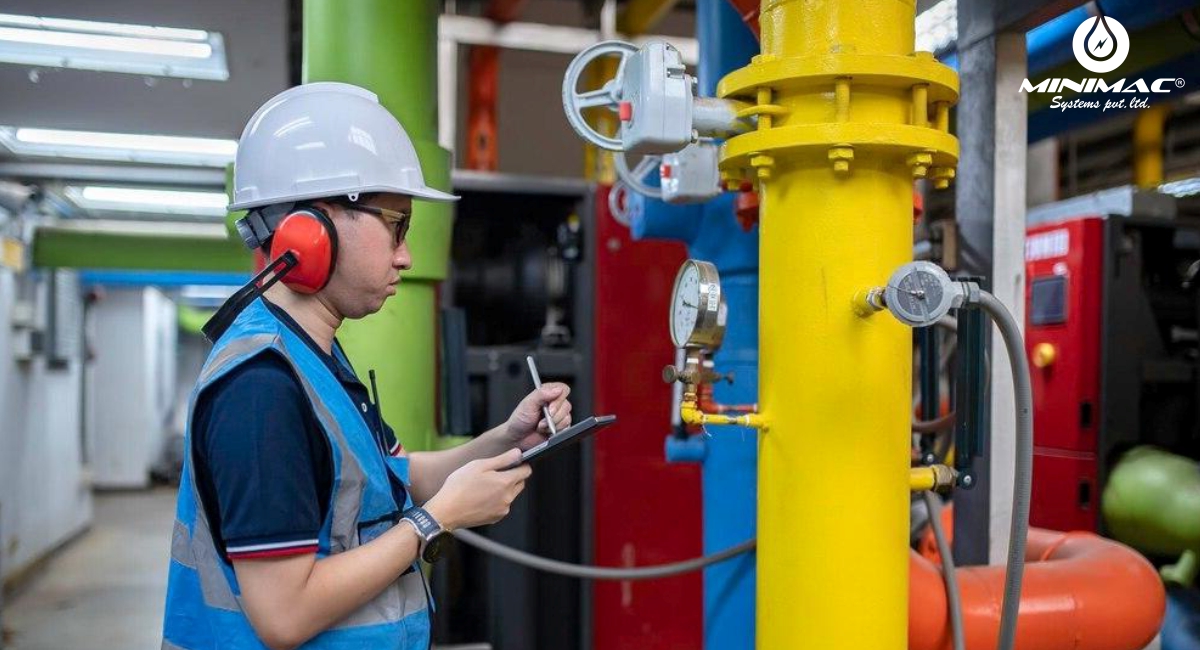
Best Practices for Oil Filtration Maintenance
Proper maintenance is essential for optimal oil filtration performance:
- Regular Filter Replacement: Adhere to the manufacturer's recommendations for filter element replacement.
- Monitor Pressure Drop: A sudden increase in pressure drop indicates a clogged filter and requires replacement.
- Integrate into Maintenance Schedule: Incorporate oil filtration maintenance into your overall equipment maintenance plan.
Case Study: Minimac's Oil Filtration Solution
A compelling example of oil filtration's impact is a polypropylene plant in Jamnagar, India. The plant faced significant contamination issues in its newly installed compressor and pipelines. Minimac's advanced oil filtration system, the FS 500, effectively removed contaminants, preventing potential equipment failure, reducing downtime, and saving millions of rupees.
Conclusion
Oil filtration is a critical component of equipment maintenance. By investing in a robust filtration system and adhering to best practices, you can significantly enhance your equipment's performance, longevity, and overall efficiency. By understanding the intricacies of filter media and system design, you can optimize the effectiveness of your oil filtration process.
Remember: Clean oil is the key to unlocking your equipment's full potential.