Water in Oil: The Hidden Threat to Your Machinery's Lifespan.
Introduction
Water contamination in oil is a major issue that can go unnoticed in many industrial settings. Oil is critical for lubricating machinery, but the presence of water reduces its effectiveness and can lead to severe mechanical damage.
Water in oil is often described as a "hidden threat" because it can be difficult to detect early, but it causes long-term harm to equipment. This issue affects a wide range of industries, from manufacturing to power generation.
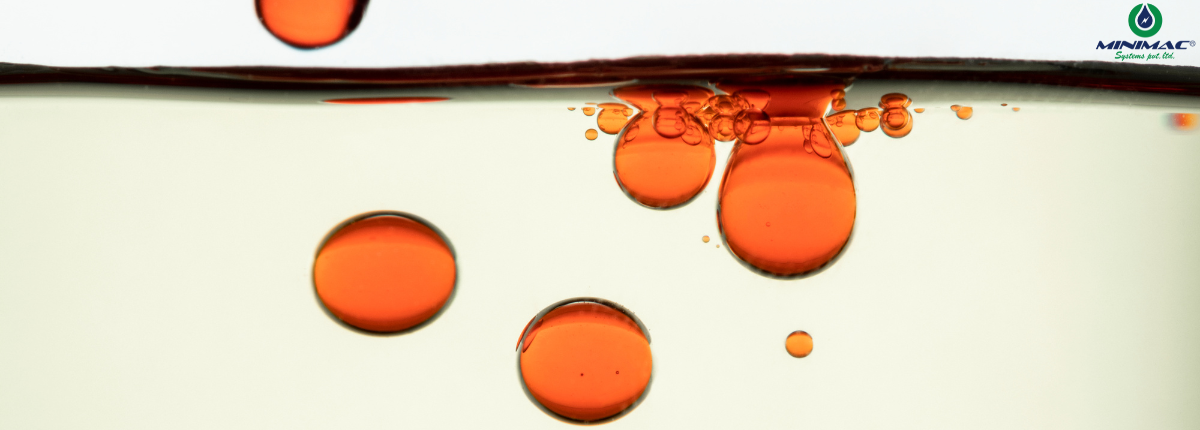
The goal is to educate the reader on how water gets into oil, why it’s dangerous, and what steps can be taken to detect, prevent, and remove it. By addressing this issue, businesses can save on maintenance costs and extend the life of their machinery.
What Causes Water Contamination in Oil?
- Condensation: Machinery often experiences temperature changes, especially when operating in environments with fluctuating humidity levels. When machinery cools down after operating at high temperatures, condensation can form inside oil reservoirs, introducing water into the oil.
- Leaks:Damaged seals, gaskets, or improperly fitted components can allow water from external sources to seep into oil systems. For instance, equipment exposed to rain or washing processes may allow water to leak into oil chambers.
- Poor Storage Conditions:When lubricants are stored in poorly sealed containers or environments with high humidity or rain exposure, water can easily mix with oil. Contaminated storage tanks are a frequent culprit in causing water ingress in oil systems.
- Types of Water Contamination:
- Free Water:Water that is not mixed with the oil and settles at the bottom of the container or reservoir. It’s easier to detect and remove.
- Emulsified Water:Water that is finely dispersed within the oil, creating a milky or cloudy appearance. This form of contamination is harder to separate from oil and often requires special treatment.
- Dissolved Water:Water that is fully dissolved into the oil and cannot be seen with the naked eye. Although dissolved water seems less harmful, it can still lead to corrosion and oxidation.
The Dangers of Water in Oil
- Mechanical Damage: When water is present in oil, it reduces the oil’s viscosity and its ability to properly lubricate machinery parts. As a result, metal components experience increased friction, wear, and eventual breakdown. This is particularly true in high-pressure environments like hydraulic systems or gearboxes.
- Corrosion:Water in oil accelerates rust formation on metal surfaces. Over time, even small amounts of water can cause significant corrosion, weakening components and leading to mechanical failure.
- Oxidation:Water contamination speeds up the oxidation of oil, leading to the formation of acids, sludge, and varnish. This degrades the oil’s quality and can cause blockages or reduce fluid flow within machinery, hindering performance.
- Reduced Efficiency:When water-contaminated oil circulates in machinery, the efficiency of the equipment is compromised. Pumps, valves, and bearings may work harder than usual, leading to increased energy consumption, higher operating temperatures, and more frequent repairs.
How to Detect Water in Oil
- Visual Inspection:Operators can start by visually inspecting the oil for any obvious signs of water contamination. A milky or cloudy appearance is often a clear indicator of emulsified water. Additionally, the formation of foam or the presence of water droplets on the surface of the oil reservoir can signal water contamination.
- Lab Testing:
- Karl Fischer Titration:This is one of the most accurate methods for measuring the water content in oil. It uses chemical reactions to detect even minute amounts of water in a sample.
- Crackle Test: A simpler, on-site method where a small sample of oil is heated. If it contains water, the heat will cause the water to evaporate, producing crackling sounds. Though less precise, this test is a quick way to check for water.
- On-Site Monitoring Tools:Industries can use sensors and online monitoring systems that continuously measure the water content in oil. These tools can provide real-time data, alerting operators if water levels rise beyond safe limits.
Preventing Water Contamination in Oil
- Proper Storage:Storing lubricants in controlled environments can significantly reduce the chances of water contamination. Ensure that containers are tightly sealed and stored away from humid conditions or areas prone to rain.
- Routine Maintenance: Regular checks on machinery can help prevent water ingress. Inspect seals, gaskets, and breathers to ensure they are functioning properly and haven’t been compromised by wear and tear. Replacing damaged seals promptly can prevent water from entering oil systems.
- Oil Dehydration Systems These systems are specifically designed to remove water from oil. They are essential in industries where water contamination is frequent, such as marine environments or manufacturing plants exposed to humidity
- These systems use heat and vacuum pressure to evaporate water from oil, making them highly effective for both free and emulsified water removal.
- These filters separate small water droplets from the oil, making them a practical solution for industries that need constant oil purification.
- Proactive Oil Monitoring: Implementing regular oil analysis programs can help detect water contamination early. By regularly sending oil samples to labs or using online monitoring tools, companies can prevent long-term damage to machinery.
How to Remove Water from Oil
- Vacuum Dehydration:This technique removes water by heating the oil in a vacuum environment, causing the water to evaporate without damaging the oil’s chemical properties. It is effective in removing both free and emulsified water and is often used in industries where maintaining oil quality is critical.
- Centrifugal Separation: This method uses centrifugal force to separate water from oil. As the mixture spins at high speeds, the heavier water molecules are pushed outward and separated from the lighter oil molecules. This is particularly useful for free water removal.
- Coalescing Filters: These filters work by merging smaller water droplets into larger ones, which are easier to remove. Coalescing filters are effective in removing emulsified water from oil and are commonly used in systems that require continuous oil purification.
Conclusion
Water contamination in oil is a silent but severe issue that can lead to costly repairs, reduced equipment efficiency, and shortened machinery life spans. Often undetected until significant damage has occurred, water contamination in oil can negatively impact industries across the board, from manufacturing to power generation. By understanding how water enters oil systems, whether through condensation, leaks, or poor storage industries can implement proactive measures to safeguard their machinery.
Detecting water in oil is not always straightforward, as some forms of contamination, like dissolved water, are invisible to the naked eye. However, with advanced testing methods such as Karl Fischer Titration and on-site monitoring tools, companies can catch water contamination early and prevent long-term damage. Routine visual inspections, lab testing, and the use of sensors can help operators maintain a constant watch over their oil systems.
Preventing water contamination starts with good maintenance practices, such as ensuring proper storage, regularly inspecting seals, and using oil dehydration systems where necessary. Additionally, proactive oil monitoring programs and the use of dehydration techniques like vacuum dehydration and centrifugal separation can effectively remove water from contaminated oil, restoring its performance and protecting machinery.
FAQS:
Q. What are the most common causes of water contamination in oil?
A: Water contamination can result from condensation, leaks in seals or gaskets, and improper storage of lubricants. Environmental factors such as high humidity or exposure to rain can also contribute to the problem.
Q. How can I tell if water is present in my oil?
A: The most obvious sign is a milky or cloudy appearance, which indicates emulsified water. Other signs include foam on the oil surface or visible droplets. Advanced testing methods like the Crackle Test or Karl Fischer Titration can also be used to detect water content.
Q. Why is water in oil dangerous for machinery?
A: Water reduces the oil's ability to lubricate properly, leading to increased friction, wear, and eventual breakdown of components. It also causes corrosion, accelerates oil oxidation, and reduces the overall efficiency of machinery.
Q. What are the best ways to remove water from oil?
A: Vacuum dehydration, centrifugal separation, and coalescing filters are effective methods to remove water from oil. Each method has its strengths, depending on the type of water contamination (free, emulsified, or dissolved).
Q.What Causes Water in Oil?
- Condensation: When machinery heats up and then cools down, moisture from the air can condense inside the oil reservoirs, leading to water contamination
- Leaks: Damaged seals, gaskets, or improperly fitted components can allow water to enter oil systems, especially in machinery exposed to external water sources like rain or washing processes.
- Improper Storage: Lubricants stored in open or poorly sealed containers in humid or rainy environments can easily absorb water, contaminating the oil.
- Environmental Exposure: Equipment operating in marine or high-humidity environments is at a higher risk of water entering the oil system through exposure.
Q. How to Prevent Water Contamination in Oil?
A: Flushing has several advantages in managing varnish:
- Proper Storage: Store lubricants in sealed containers away from moisture and in temperature-controlled environments. Avoid outdoor storage that exposes oil to rain or humidity.
- Routine Maintenance: Regularly inspect machinery for damaged seals, gaskets, and other vulnerable areas. Ensure that breathers and filters are functioning properly to prevent water ingress.
- Use Oil Dehydration Systems: Installing systems like vacuum dehydrators or coalescing filters can help remove water from oil and prevent contamination from accumulating over time.
- Proactive Oil Monitoring: Implement a regular oil analysis program to detect water contamination early, allowing for timely intervention and minimizing potential damage to machinery.
Q. How to detect water in oil?
- Visual Inspection: Look for signs like a milky or cloudy appearance, foam, or visible water droplets in oil reservoirs.
- Lab Testing: Techniques like Karl Fischer's Titration and simpler methods like the crackle test help detect water content.
- On-Site Monitoring Tools: Continuous sensors and monitoring systems can provide real-time data on water levels in oil.
Q. How to test for oil in water?
A: To test for oil contamination in water, methods such as infrared spectrophotometry, gravimetric analysis, and gas chromatography are often used. On-site tests may include using oil-in-water analyzers to provide quick readings.
Q. How to check the water content in oil?
- Karl Fischer Titration: A precise lab-based test that quantifies water content in oil.
- Crackle Test: A quick, on-site method where a heated oil sample reveals water presence through crackling sounds.
- Online Sensors: These tools continuously measure water content and provide alerts if levels exceed safe limits.
Click here to learn more about oil condition monitoring equipment - Click here