What is Oil Filtration? Importance, Types, and Benefits Explained
Introduction
Oil filtration is a crucial process in maintaining the efficiency and longevity of machinery, engines, and hydraulic systems. It involves removing contaminants, such as dirt, water, and metal particles, from oil to ensure optimal performance. In a world where machinery operates under increasingly demanding conditions, understanding oil filtration becomes paramount for industries relying on lubrication systems. This article delves into the nuances of oil filtration, exploring its importance, types, processes, benefits, challenges, and innovations in the field.
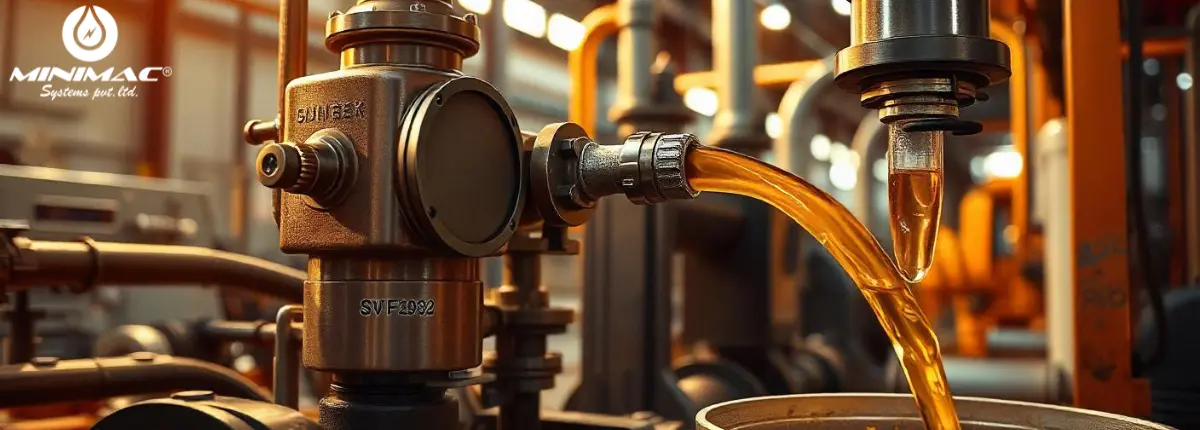
Understanding Oil Filtration
Oil filtration refers to the method of purifying oil by removing impurities that can degrade its quality. Contaminants can enter the oil through various means, including wear and tear of machinery components, environmental factors, and improper handling during oil changes. The primary goal of oil filtration is to enhance the oil’s performance, thereby protecting the machinery and extending its service life.
3. Importance of Oil Filtration
Effective oil filtration is essential for several reasons:
- Machinery Protection: Contaminants in oil can cause excessive wear and tear on components, leading to breakdowns and costly repairs.
- Enhanced Efficiency: Clean oil ensures that machinery operates at optimal efficiency, reducing energy consumption and improving overall performance.
- Extended Oil Life:Proper filtration prolongs the life of the oil, reducing the frequency of oil changes and lowering maintenance costs.
- Environmental Responsibility:Efficient oil filtration reduces waste and minimizes environmental impact by extending the life of lubricants and preventing spills.
Types of Oil Filtration
There are several types of oil filtration system, each designed to address specific needs:
- Mechanical Filtration:This type utilizes physical barriers, such as filters, to capture particles. Common examples include paper filters, spin-on filters, and mesh filters.
- Centrifugal Filtration:This method employs centrifugal force to separate contaminants from oil. It is particularly effective in removing larger particles and sludge.
- Magnetic Filtration:Magnetic filters attract ferrous contaminants, ensuring that metal particles are removed from the oil, thus preventing damage to sensitive components.
- Chemical Filtration:Chemical processes can also purify oil by breaking down contaminants or changing their chemical properties to make them easier to filter out.
- Vacuum Filtration:This technique uses a vacuum to draw oil through a filter medium, effectively removing fine particles and water.
Hydraulic Oil Filtration
Hydraulic oil filtration is essential for the smooth operation of hydraulic systems, which are widely used in various industries, including construction, manufacturing, and transportation. Hydraulic systems rely on pressurized oil to transmit power, and any contamination can lead to decreased efficiency, increased wear, and potential system failure.
- Filtration Methods:Hydraulic oil filters are typically designed to remove particles from the oil before it reaches critical components. These can include return line filters, pressure filters, and offline filters.
- Importance: Maintaining clean hydraulic oil is vital to ensure the system's reliability, prevent downtime, and extend the lifespan of hydraulic components.
- Filtration Techniques:Common methods include depth filters, surface filters, and centrifuges that can effectively remove particulate matter, oxidation byproducts, and moisture.
- Significance:Clean lube oil not only improves engine performance but also enhances fuel efficiency and reduces harmful emissions. Regular lube oil filtration can significantly extend the life of engines and machinery.
- Key Filtration Methods:Turbine oil filtration often involves multi-stage filtration systems that use coalescing filters and fine filters to remove water and particulates.
- Critical Role:Effective turbine oil filtration is critical for maintaining the operational efficiency of turbines, reducing maintenance costs, and ensuring the reliability of power generation.
- Oil Collection:Contaminated oil is collected from the machinery.
- Pre-Filtering: Larger particles are removed using a coarse filter or screen.
- Filtration: The oil is passed through a filter medium that captures smaller particles and impurities. Depending on the type of filtration used, this could involve mechanical, centrifugal, magnetic, or chemical processes.
- Quality Testing:After filtration, the oil is tested for quality and cleanliness to ensure it meets the required specifications.
- Reintroduction:The clean oil is then reintroduced into the machinery, ensuring optimal performance and protection.
- Reduced Maintenance Costs:By minimizing wear and tear on machinery, effective filtration reduces the need for frequent repairs and replacements.
- Improved Equipment Performance:Clean oil contributes to better machinery performance, leading to higher productivity and efficiency.
- Cost Savings:Extended oil life reduces the frequency of oil changes, saving both time and money for organizations.
- Environmental Benefits:By ensuring efficient use of resources, oil filtration contributes to environmental sustainability, reducing waste and pollution.
- Contamination Sources:Identifying and mitigating various contamination sources can be difficult, requiring regular monitoring and maintenance.
- Filter Selection:Choosing the right type of filter for specific applications can be challenging, as each type has its strengths and weaknesses.
- Operational Conditions:Extreme operational conditions, such as high temperatures and pressures, can impact the effectiveness of filtration systems.
- Cost of Equipment:While oil filtration systems can save money in the long run, the initial investment in high-quality filtration equipment can be substantial.
- Smart Filtration Systems:IoT-enabled filtration systems can monitor oil quality in real time, alerting operators to potential issues before they escalate.
- Nanofiltration:Utilizing nanotechnology, new filters can capture even smaller particles, enhancing oil purity and performance.
- Self-cleaning Filters:These innovative filters can remove contaminants automatically, reducing maintenance requirements and downtime.
- Biodegradable Filters:Biodegradable Filters:Environmentally friendly filtration options are being developed, reducing the ecological impact of traditional filters.
Lube Oil Filtration
Lube oil filtration focuses on purifying lubricating oils used in engines and machinery. Lube oil helps reduce friction between moving parts, preventing wear and ensuring smooth operation.
Turbine Oil Filtration
Turbine oil filtration is specifically designed for steam and gas turbines used in power generation and industrial applications. Turbine oils must be free from contaminants to ensure efficient operation and prevent damage.
The Oil Filtration Process
The oil filtration process typically involves the following steps:
Benefits of Oil Filtration
Implementing effective oil filtration systems offers numerous benefits:
Challenges in Oil Filtration
Despite its benefits, oil filtration faces several challenges:
Innovations in Oil Filtration
Advancements in technology are continuously improving oil filtration processes:
Conclusion
Oil filtration is a critical aspect of machinery maintenance and operation, ensuring optimal performance and extending the lifespan of lubricants. By understanding the various types of oil filtration, including hydraulic oil, lube oil, and turbine oil filtration, the processes involved, and the benefits they offer, industries can make informed decisions that enhance productivity, reduce costs, and promote sustainability. As technology continues to evolve, innovations in oil filtration will undoubtedly lead to even greater efficiencies and environmental benefits.
FAQS:
Q: What is oil filtration?
A: Oil filtration is the process of removing impurities from oil to enhance its performance and protect machinery.
Q: Why is oil filtration important?
A: It is important for protecting machinery, improving efficiency, extending oil life, and reducing environmental impact.
Q: What are the types of oil filtration?
A: Types include mechanical, centrifugal, magnetic, chemical, and vacuum filtration.
Q: What is lube oil filtration?
A: Lube oil filtration purifies lubricating oils used in engines and machinery to reduce friction and prevent wear.
Q: What is turbine oil filtration?
A: Turbine oil filtration is designed to purify oils used in turbines, ensuring efficient operation and preventing damage from contaminants.
Q: How does the oil filtration process work?
A: The process involves collecting contaminated oil, pre-filtering, filtering through a medium, testing quality, and reintroducing clean oil.
Q: What are the benefits of oil filtration?
A: Benefits include reduced maintenance costs, improved equipment performance, cost savings, and environmental benefits.
Q: What challenges does oil filtration face?
A: Challenges include contamination sources, filter selection, operational conditions, and the cost of equipment.
Click here to learn more about oil filtration systems - Click here