Oil Reclamation project for the largest oil refinery in WB, India
A critical oil reclamation project for the largest oil refinery with a capacity of 8 million tonnes per year in West Bengal, India.
Synopsis
The lube oil used in various industrial equipment such as pumps, compressors, turbines, blowers, turbo generators, recycle gas compressors, wet gas compressors, and coke cutting pumps had critical contamination levels initially. The problem was caused by poor maintenance by a previous service vendor, resulting in the presence of moisture and impurities in the oil tank. To address the issue, Minimac Operations and Maintenance Service (MOMS) carried out a timely service operation to help the plant bring down the moisture count and remove impurities from the oil tank. Before oil purification, NAS ≥ 12, Moisture ≥ 650 PPM; after oil purification, NAS < 5 and Moisture < 200 PPM This helped to improve the quality of the oil used in the equipment and ensure the smooth operation of the plant.
Problems
The oil was contaminated with moisture and mechanical impurities due to insufficient maintenance, which could lead to equipment failure and downtime. The presence of these impurities in the oil could also cause damage to the equipment, reduce its lifespan, and decrease its efficiency. It was essential to address this problem by implementing proper maintenance practices, such as regular oil changes, filtration, and moisture control, to ensure that the industrial oil is clean and free from contaminants. Failure to address this issue could lead to increased costs as well as production losses due to downtime.
Client’s Requirement
- The target moisture level must be below 200 PPM.
- Target NAS class must be maintained better than NAS class 5.
Solutions
- Minimac Systems examined the oil circulation system, which consisted of high impurities.
- Machine used: FS 80 LPM - 2 units; FS 40 LPM - 1 unit; FS 20 LPM - 1 unit.
- NAS class < 5 and < 200 PPM moisture level was achieved.
Cost Saving
This plant managed to save:
- Immediate tangible benefit = ₹9 Cr.*/ $90 Million* * considering the base price of oil as ₹150/lts /$1.83/lts.
- Intangible benefits = Equipment reliability - less breakdowns - minimum equipment outage - reduced downtime - minimum hamper to production line.
CO2 e Saving
72,00,000 kg of CO2 e / 7.2 gigagrams of CO2 e.
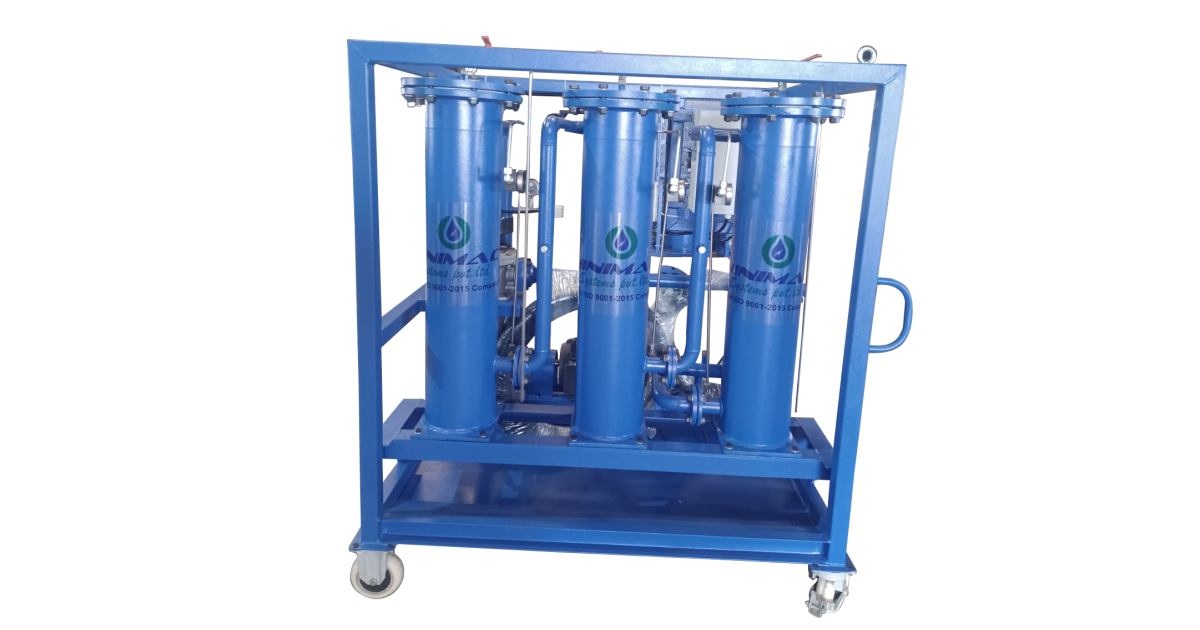
Benefits
- The reliable operation of the system and trouble-free operation of machines.
- Sustainable performance of the overall process.
- Less Breakdown.
- Elimination of new compressor cost.
- Reduction in the possibility of product degradation due to lack of proper filtration.
- Timely Execution.
Feedback
Minimac believes in delivering the best experience to the clients with result-oriented project execution, hence, as a result, the project was extended further.
Subscribe to our YouTube Channel and be a part of our Journey - Click Here