Preserving 35 kL of Prime 46 Oil from Solid and Moisture Impurities
Minimac Rescues Bihar Power Station : Customized Solution for Solid Contamination and Moisture Wins.
Synopsis
In Begusarai, Bihar, a 720 MW coal-fired power station owned by a major PSU recently faced high Solid Contamination and Moisture Levels in two tanks each with 115 MW power potential. To avert disruption, Minimac provided a customized solution, deploying a specialized machine to lower NAS levels and address moisture and solid contamination saving the plant from a potential failure.
Initial Findings
The power plant's poor operational condition had resulted in the oil degrading to its maximum limit, physical inspection revealed highly contaminated oil with various unwanted contaminants such as sludge, metal parts, insects, dirt, etc.
Problems
Two primary lubrication oil tanks, each with a substantial 115 MW power potential, experienced significant contamination from solids and moisture. Utilizing the contaminated oil to initiate the turbine posed a critical risk of tripping the overall system, leading to potential catastrophic failures.
Client’s Requirement
- To Purify 15 kL & 20 kL of Prime 46 Oil from the respective tanks.
- To remove Moisture and Solid Contaminants.
- To Achieve NAS ≤ Class 8.
- To Achieve Moisture ≤ 500 PPM.
- Customized Solution.
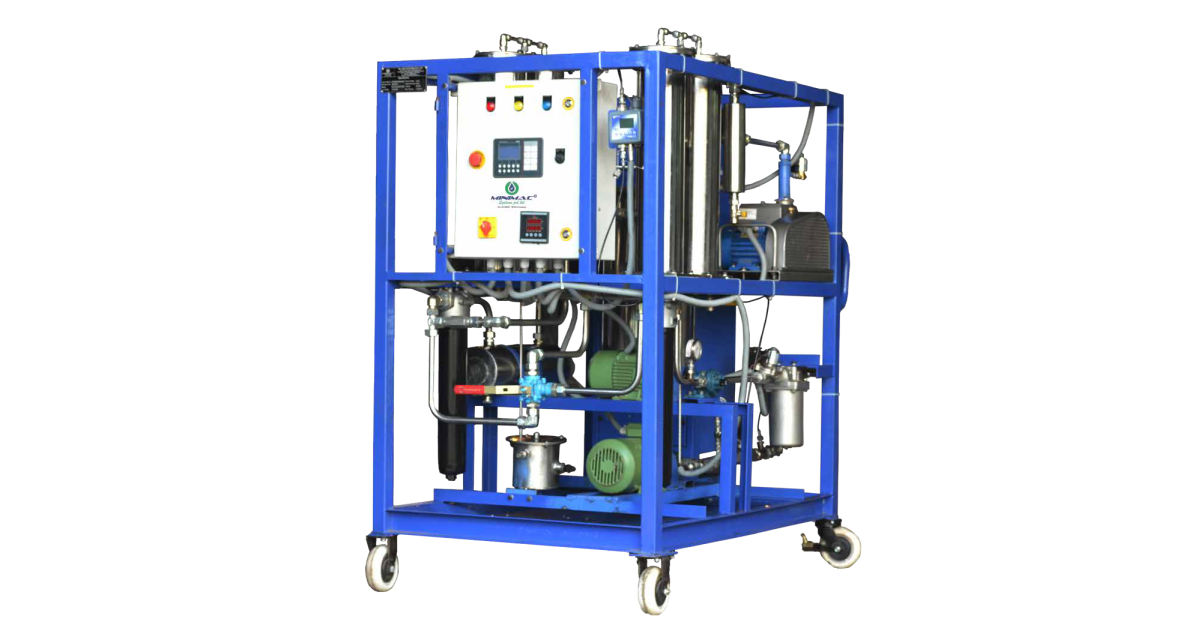
Solutions
Deploying Minimac’s customized machine at the site along with trained and skilled engineers.
- Oil filtration system(150 LPM & 200 LPM) to bring the NAS level of oil to the desired range.
- Low Vacuum Dehydrator (100 LPM) to maintain consistent moisture levels in the oil using the vacuum dehydration ensuring smooth turbine operation in its active state.
- Our Service Engineer installed the equipment and provided training on its operation and effective handling to the client's team.
- Job executed within a limited time-span on the running unit without hindering the client’s operations and oil tanks.
Value Type | Oil Tank under UNIT 7 (15kL) | Oil Tank under UNIT 8 (20kL) | ||
---|---|---|---|---|
Before | After | Before | After | |
NAS | Class 12 | Class 8 | Class 12 | Class 8 |
Moisture Level | 13000 PPM | 64 PPM | 700 PPM | 42 PPM |
Cost Saving
This plant managed to save:
- Cost of Oil Replacement: ₹75 Lakhs. Approx
- Cost of Downtime: ₹1 Cr. Approx
CO2 e Saving
4,20,000 kg of CO2 e / 0.42 gigagrams of CO2 e
Benefits
- Prevented the environment from harm by averting the emission of 4,20,000 kg of CO2e.
- Saved 35 kL of Oil from being incinerated.
- Extended Oil Life.
- Reduced NAS & Moisture Levels.
- Elimination of Oil Replacement Costs.
- Task Successfully performed without any shut downs and in a limited amount of time.
- No Accidents/ Spillage.
- HSE Norms Fulfilled Diligently.
Abbreviations Used
- kL : kilolitre
- kg : kilogram
- MW : Megawatt
- NAS : National Aerospace Standard
- LPM : Litres Per Minute
- PPM : Parts Per Million
- HSE : Health, Safety & Environment
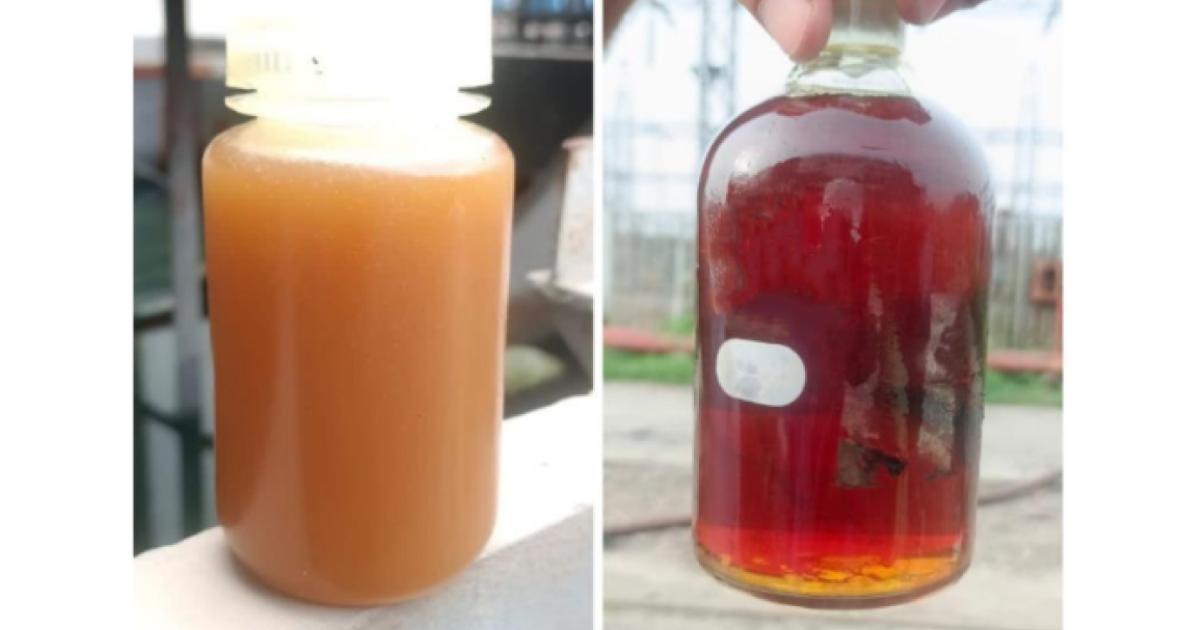
Oil Visuals : Before & After
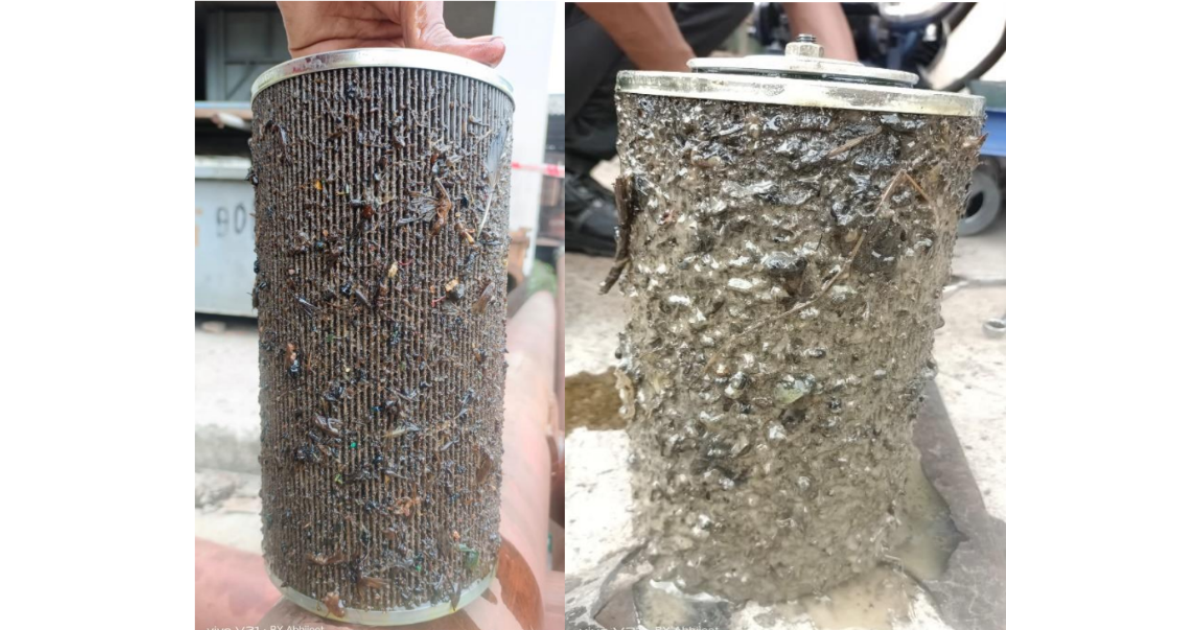
Filter Visuals : Before
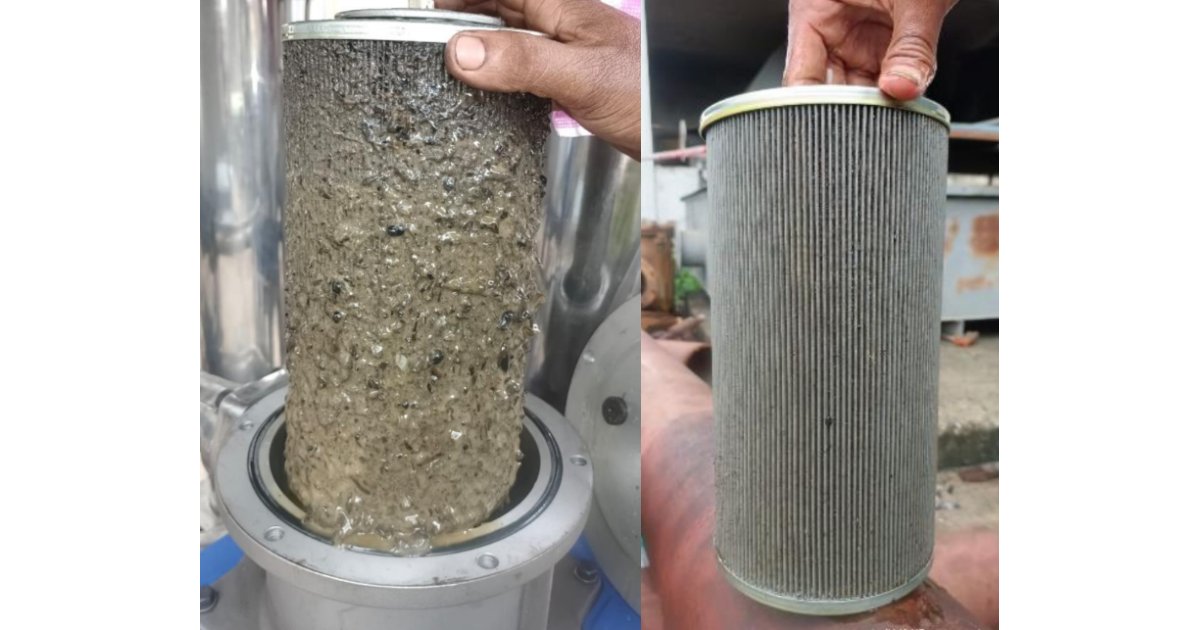
Strainer Conditions Before Filtration Filter Visuals : After
Subscribe to our YouTube Channel and be a part of our Journey - Click Here